***************************
Please Notice
For the current version of the bus and rack design please see this post.
This introductionary post here uses a different, older bus design, but the overall idea for the Modular Extensible PnP Factory System stays the same, so just read on

***************************
Foreword
Hi there

I've been playing Factorio now for quite some time and I have unlocked every tech, fiddled around a bit and am now in a phase that I would call maybe "mid-early to mid" factory design stage.
Assuming this is a very subjective opinion I would describe it for myself as "not placing everything all over the place anymore" and having reached a stage in which trains become interesting and valuable.
I am not yet in the need for dual/quadruple blue belts, usually dual red (~= single blue, quadruple yellow) or even single red (~= half blue, dual yellow) belts are sufficient for my demand of produced items.
Because Factorio is constantly triggering my desire to aim for efficient but still extensible, modular designs I have come to the development of, what I would call, "modular factory design consisting of exchangeable facility appliances attached by a standard interface to a common bus system".

The designs created from this philosophy have already experienced some iterations and are now in a state that I call "preliminary publishable"

Design philosophy
As already stated above the aim for that extensible factory is to be modular. Therefore the factory consists of several different modules that each have a very specific function.
To get all the different facilites work with each other there is a kind of protocol or interface necessary (or just a huge logistics network, but where is the fun in that?

Without further ado here's a small example of what I'm talking about here:
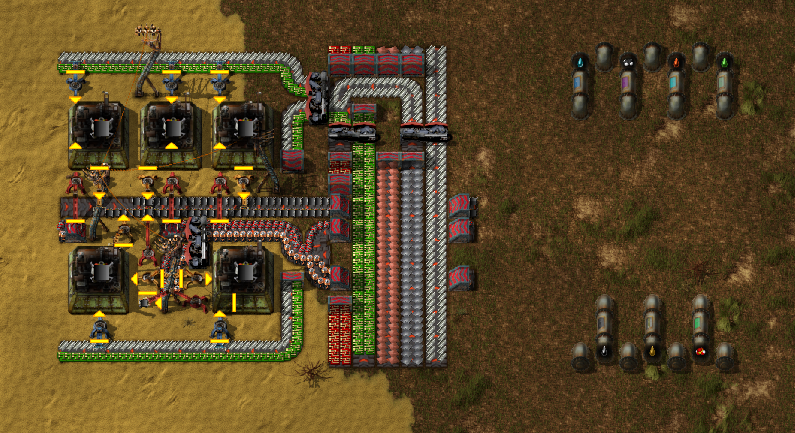
This is one of those factory modules (with not much going on

One of those "rows" is called rack.
A rack is, by design rule, always 13 tiles high.
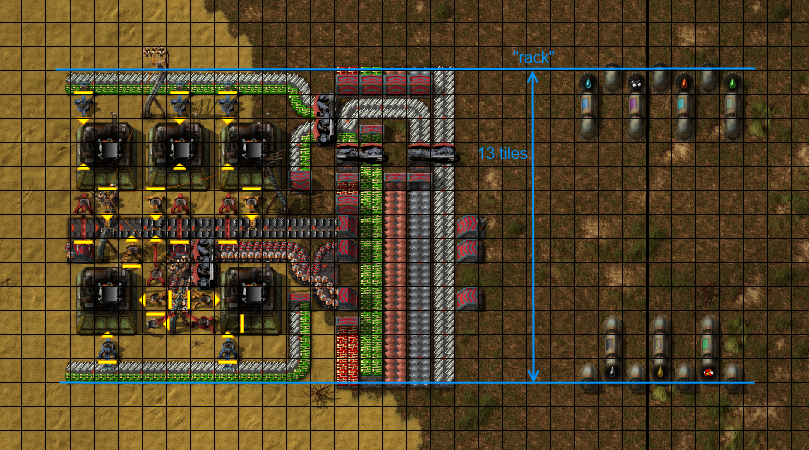
One rack usually has only one type of facility in it, with matching belts and pipes to split off used items and fluids.
As the belts and pipes have a standardized filling and rack height is standardized it is possible to swap out a whole production row by deconstructing it and replacing it with something else in case of limited space or ceased demand (e.g. engines, etc.):
Such a production row consists of three compartments (from right to left):
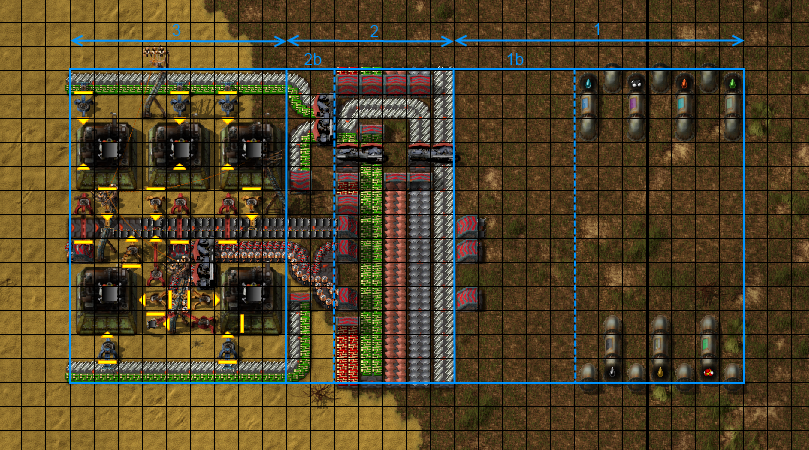
1. Pipes
The pipes are used to get fluids, produced by some module, to other modules. Think about a bus system for fluids.
There are always seven pipes in parallel, placed without a gap. They are always used for these fluids (left to right):
Water, Oil, Petrolium Gas, Light Oil, Heavy Oil, Sulfuric Acid, Lubricant.
That seemes like a good ordering to me and coincidentally is also the same here, nice as a reminder.
1b. "Fluid Connector"
Some free space between the pipes and the belts. This space is used for routing the fluids from the supply pipes on the left to the facility.
Is also used for I/O-belt-routing or further addiitons like additional power poles, roboports for blueprint placing, etc.
It's width is always 5 tiles.
2. Belts
Next to the pipes are the belts. They transport a continous stream of items from the bottom to up.
They are red belts, placed without a gap. The items in these belts are always (left to right):
Advanced (red) Circuits, Electronic (green) Circuits, Copper, Iron, Steel
Remarks:
Pipes and belts always have the same position and both are only needed once per rack.
Thus they can be considered as one building block and are therefore stored as a single blueprint to interface the facility to the bus system. This combined block is called a "connector"
Sometimes pipes or belts are not used for any racks above or below a rack.
In this case it is legitimate to remove or disconnect the unneeded pipes/belts to conserve resources stored on belts or in pipes.
So you can have rows having only rows or only pipes (or neither).
However the overall layout must be retained in case belts or pipes have to be rebuild when demand arises.
2b. "Solid Connector"
Connects the items on the support belts with the facility by splitting off required resouces and routing the side(un)loading belts of the more specialized ingrediends and finished products.
The width is dynamic as the only following to the left compartment is the facility itself and routing of all the belts and pipes isn't always the same.
3. Facility
This is the production logic where something is made from the provided resources, be it fluids or items.
The clou here is, this facility is (and by design rule MUST be) able to be repeated as often as desired to the left.
So you can have multiples of the same production facility, connected by one belt and one pipe compartment:
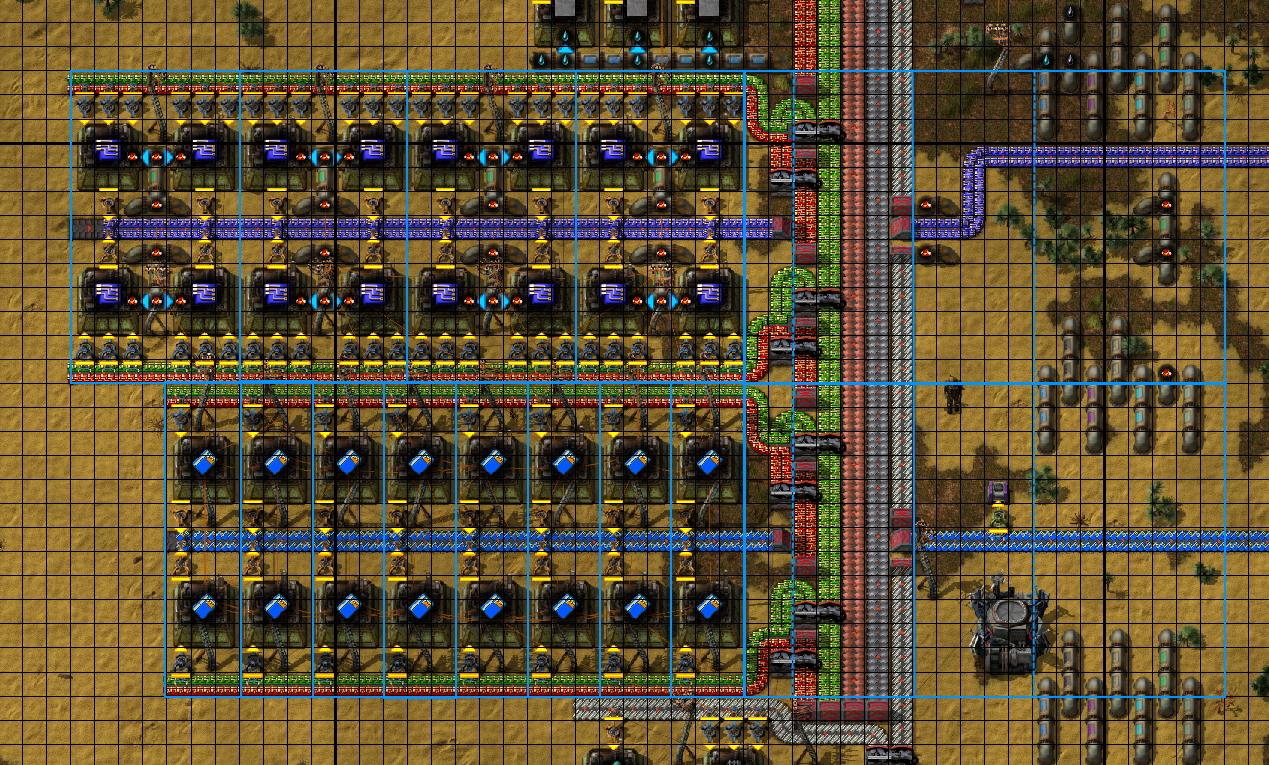
(This example is a little "special" as the green circuit production facilities can overlap to conserve some space

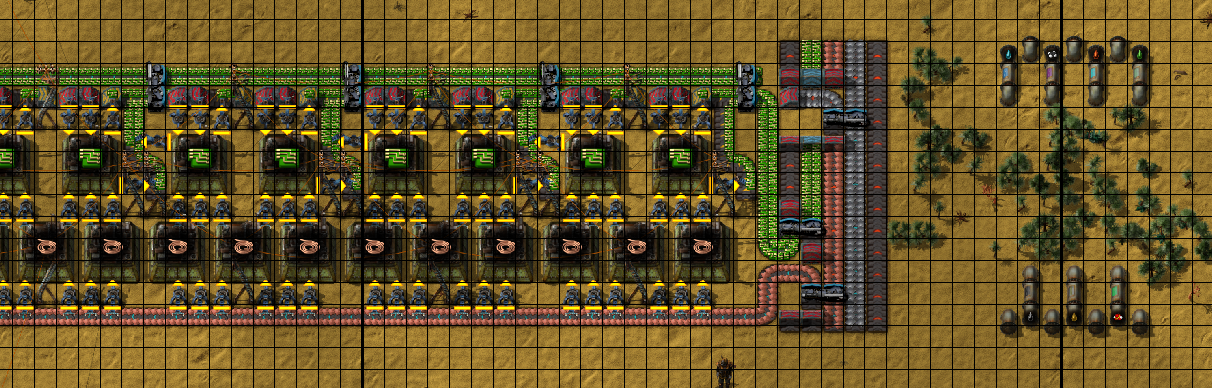
Designing such a production facility must have extensibility in mind from the beginning, so needed resources are passed along the row to potentially more production facilites, same goes with created items or fluids, they have to be fed out of the rack in such a way additional facilites contribute to the same output line.
If the facility needs or produces items which are not transported on the bus belts, these resources are "side fed" in and out.
Side fed items also have to obey the rule to facility extensibility, means multiple facilites along the line must get those items, also, and not only the first:
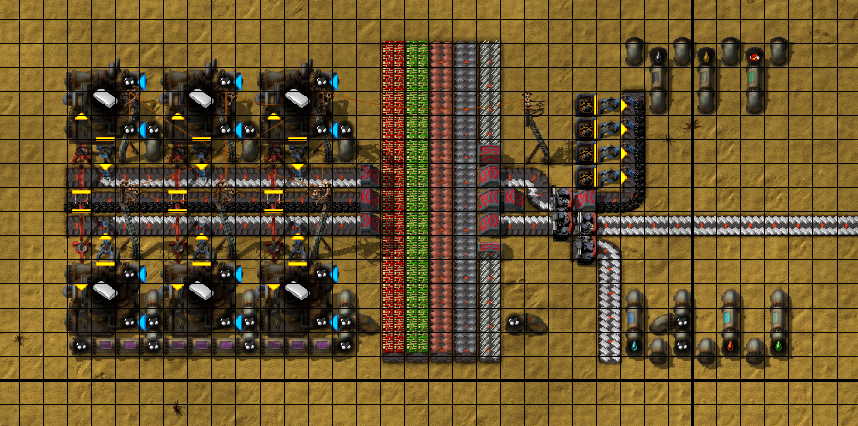
Here you can also see how fluids are split off the pipe bus and fed into the facility.
By now you should be able to see each compartment at a glance

Rules overview
So these are the design rules:
Format:
- a rack MUST always be 13 fields high. It is never shorter and never longer.
- a standardized belt and pipe system exists. Its connectors to the north and to the south MUST be preserved
Consistency:
- belts or pipes MUST NOT swap positions. Their position MUST be respected (see above screenshots for dimensions)
- the topmost tile row MUST NOT contain any pipes that could be able to connect to the north, which would then be the lowest tile row of the rack above this one. This is IMPORTANT! Not respecting this rule can result in unexpected fluid mixing, poisioning the whole fluid system! (it's a pain to get those pipes clean again)
- belts and pipes MAY be omitted if all racks above or below don't need either. When omitting it MUST be possible to rebuild the belts and pipes from the original blueprint (read: don't put stuff there that would interfere when pasting the blueprint over the stipped down connector again)
Ideology:
- facilities should product items as fast as possible. Yes, everything can be done with yellow inserters but using the right inserter and the right amount can speed up production. Where this leads to can be seen below at the capsule facility

Blueprint shelf
Another charme of this modular rack-design is that every rack can be stored as blueprints, ready to be copy-and-pasted to whereever you need it to be, with all intermediate product facilities in reach as they are also just racks.
So it is possible for everyone to design such a rack for themselves and trade their designs and "recipes" as long as they obey the above rules to ensure interchangeability.
For me obeying these rules and building facility after facilitry is a nice exercise and sometimes requires clever solutions without me feeling the rules being too restrictive.
I enjoy my plug and play factory ^^

Still to write
- mass storage of iron and copper plates
- main bus system for iron and copper plates and how to attach these to the rack-system 5-belt bus system
- mass storage of oil barrels any why it's a good idea to bottle up oil to side-feed the oil barrels in to fill the oil pipe (and not store oil in a tank)
- why ores are processed right where they are extracted and only plates get transported to the unified extensible storage
- unified extensible train stations for loading/unloading/both-in-one
- blueprints