But it seems to me (unless I've missed something big) that there is a really simple solution.
Old belt compression method used the following methods, the underground and splitter inserter (not shown) used a speed work around and the side loading was loading into a belt without sufficient space.
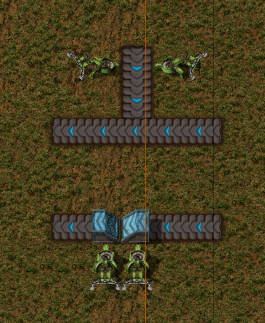
These methods always have felt like small exploits but things we have done because we are lazy...
0.16 has a few new/old method(s) to ensure compression, all we need to do is modify the designs...
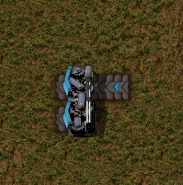
This I think will become the default output method to build your new designs around, it's simple and effective.
I will post a few designs below for various assembler setups and even an early game smelter setup. (They are all tilable)
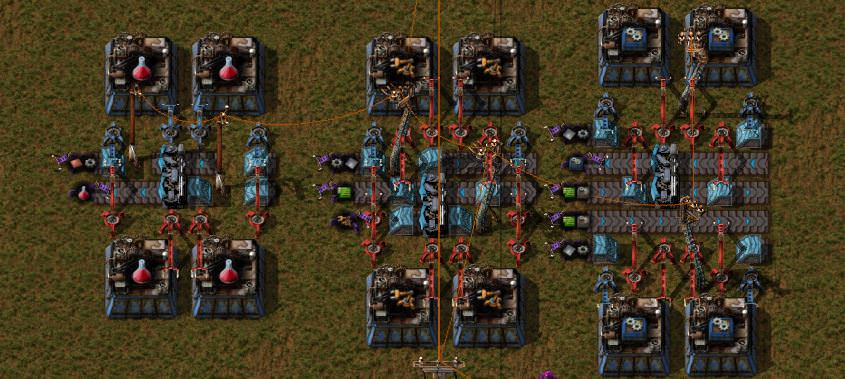
here we have (left to right) 1in/1out, 2in/1out, 2^2in/1out.
The Red Science and yellow Inserter are capable of filling the output belt to full density, the Assembler 2's is not (due to lack of input resources).
Smelter Below
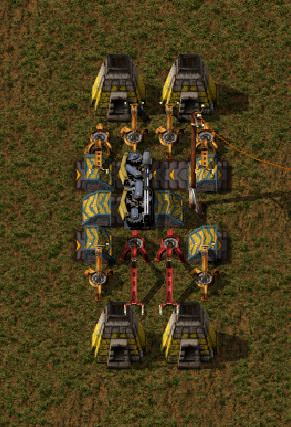
They are all built around a simple concept of output onto an isolated belt then split it into the main output.
Train Stations....
I have a couple of options they both fill 4 belts to full compression without need for too many upgrades.
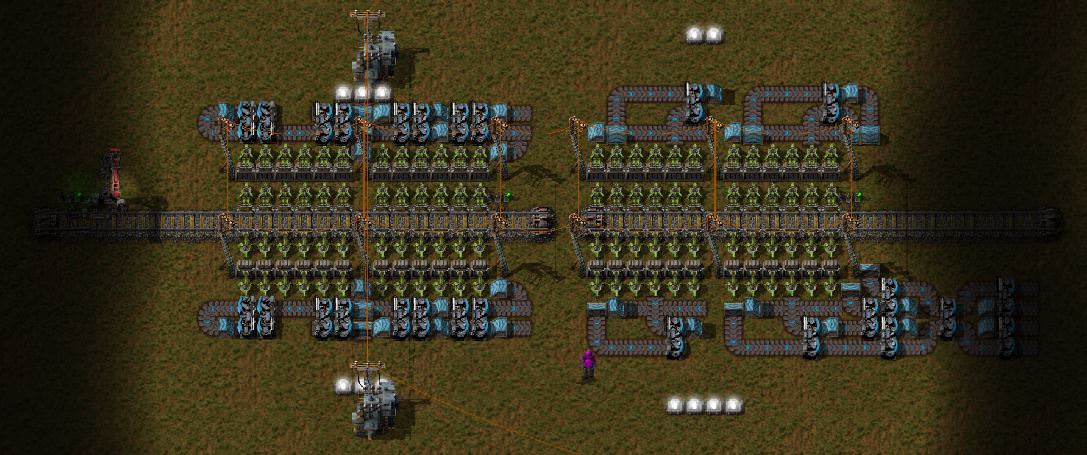
They essentially have the same goal, send 2 belts with more ore than 1 can handle into a splitter then pull 1 output. end result is a fully compressed belt.
These solutions are not complicated or require lots of tech or circuits.
So given we can mine, smelt, assemble, unload from trains without compression issues, can I ask what the problem with compression is?
Footy