For a long time I didn't understand the real use of beacons.
I thought they were to hyper speed a mega base, and for bases that were designed for rocket a minute.
In my case, I'm not often interested in rocket a minute nor mega bases. So I've mostly ignored speed modules and beacons.
Also, with the new nuclear plants, power is not a problem, so I ignore the efficiency modules.
But, the free goods from productivity modules is hard for me to ignore, so I apply prod 3 modules everywhere...
That slows down things, but the factorio answer to that is more, so build 2 factories with instead of 1.
The real reason for beacons is that they make building your factory cheaper, you need fewer assemblers and fewer modules if you use beacons.
There was a post on the math of productivity modules that gave me a clue viewtopic.php?f=134&t=5705. This is a very good post and one I refer to frequently.
That hint in DaveMcW's post kept bugging me, and eventually I took a look at speed modules in beacons with prod modules in assemblers. It's really more than a hint, but I didn't pay much attention to it the first time.
The numbers are amazingly good.
For example, a level 3 assembler using 4 prod 3 modules (PM3) runs at speed .5 and makes .1 high tech beaker a second (on average).
If you want 1 a second you need 10 of them.
If you do something like this:
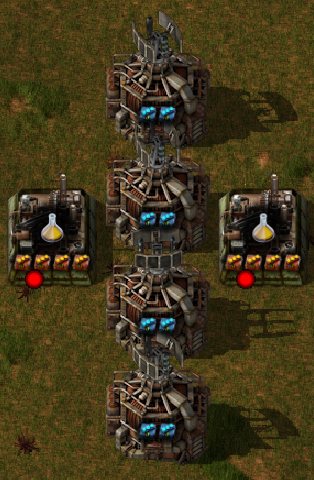
Those 2 assemblers each run at speed 3, so they make .6 beakers a second, and to get 1 a second you need slightly less than 2.
The 2 assemblers use 8 PM3s, and the 4 beacons use 8 SM3s (speed module 3s), for a total of 16 modules 3's vs 40 needed for 10 assemblers in the case if 1 high tech beaker per second.
Since level 3 modules are expensive, it really helps to save those 24.
If you make this instead:
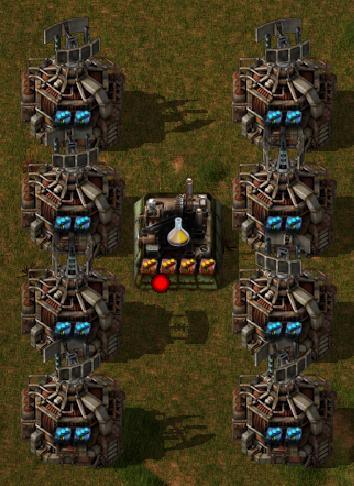
That 1 assembler runs at speed 5.5 so it makes 1.1 beakers a second.
That uses a total of 4 PM3s and 16 SM3s, which while it's more than the prior case, it does allow other types of factories to exist beside it and split the total cost.
That's with one assembler. When you add additional assemblers the costs go down a lot, because for each additional assembler you only have to add 1 or 2 beacons. They share the beacons from the existing assembler, so in the 4 beacon case the first assembler saves 24 modules, the second saves 30.
In the 8 beacon case the first saves 20, the second saves 32. This assumes you add the assemblers in a line each touching the next, that can require some creative designs.
If you don't use modules or use other than productivity modules, then beacons are not as effective because the counter of slow production to speed makes the whole setup much more effective.
For power and pollution, if you compare 4 PM3s with and without beacons the 8 beacon setup uses about 1/2 the power, and about 1/5th the pollution (assuming clean electricity).
There are some things to be aware of. If your factory is not running full time, assemblers will decrease their power usage, but beacons will not, so an idle factory with beacons will still use a lot of power.
The other thing to be careful about is the feeding of fast assemblers. especially for 1/2 second recipes a 5.5 speed factor means it finishes in less than .1 seconds, so keeping them fed 100% is impossible since the assembler will trigger a request when it gets below 2x ingredients, and it takes longer to load them than 1/3 a second. A stack inserter (or 2) will keep that fairly infrequent however. 1 second recipes can be kept full if you can keep enough material at the inserters, but that may require stack inserters or multiple inserters. Emptying shouldn't be a problem for most recipes, although if you have a wire (1/2 second 2 wires per recipe) making 30.8 (4/sec default, time 5.5 plus 40%) wires a second, you'll need 2 stack inserters going to a chests.
To a lesser degree this applies to labs and furnaces as well. I do recommend it for labs because it does reduce module needs and research is expensive (see DaveMcW's post). I don't recommend it for furnaces, they only take 2 modules and they're so slow that productivity isn't generally worth it, but if you do put prod mods in your furnaces you should use beacons as well, as that lowers the total number of modules required.