Steel Furnace setup: 3-express belts of output
Forum rules
Circuit-free solutions of basic factory-design to achieve optimal item-throughput
-
- Fast Inserter
- Posts: 154
- Joined: Fri Jul 15, 2016 1:44 am
- Contact:
Re: Steel Furnace setup: 3-express belts of output
Confirmed that 18-tiles high is what this pattern can do for 3-output belts.
The issue is that the "middle" belts will require more room. That probably is solvable... but 18x70 is definitely an underestimate, but I'm sure I don't need 18x140. Ideally, this pattern comes out to be 18x110 or so at full scale (I got 107-tiles wide and a 4-furnace "wide" setup in my original design, so that'd become ~1980 if I can solve all of the issues that arise from the half-dense middle belts.
The issue is that the "middle" belts will require more room. That probably is solvable... but 18x70 is definitely an underestimate, but I'm sure I don't need 18x140. Ideally, this pattern comes out to be 18x110 or so at full scale (I got 107-tiles wide and a 4-furnace "wide" setup in my original design, so that'd become ~1980 if I can solve all of the issues that arise from the half-dense middle belts.
- Attachments
-
- 18xWhat.png (962.44 KiB) Viewed 15211 times
Re: Steel Furnace setup: 3-express belts of output
Well, you need 70 furnaces per blue belt. So your setup will produce one blue belt of output in a 12x70 footprint, not two.
But I think the combing pattern is the key to get to the most compressed design. Also I think that the 73*9 layout might actually be what gheift found, explaining his 657 figure. Need to see how it's possible.
But I think the combing pattern is the key to get to the most compressed design. Also I think that the 73*9 layout might actually be what gheift found, explaining his 657 figure. Need to see how it's possible.
But you're only feeding 1.5 belts of ore in that screenshot, so that won't be enough for the 3 belts of output.The issue is that the "middle" belts will require more room. That probably is solvable... but 18x70 for 3-express belts is... kinda looking possible right now.
Is your railroad worrying you? Doctor T-Junction recommends: Smart, dynamic train deliveries with combinator Magick
-
- Fast Inserter
- Posts: 154
- Joined: Fri Jul 15, 2016 1:44 am
- Contact:
Re: Steel Furnace setup: 3-express belts of output
Yeah, I edited my post as soon as I realized that. You got ninja'd. Sorry about that.But you're only feeding 1.5 belts of ore in that screenshot, so that won't be enough for the 3 belts of output.The issue is that the "middle" belts will require more room. That probably is solvable... but 18x70 for 3-express belts is... kinda looking possible right now.
18x110 would be ideal, if I can solve the balancing issues just like I did in my original design. Due to the significantly smaller space, I think I'd have to spend 2 to 4 tiles to solve it, so maybe 18x115 ?? If I can get 18x111, then it'd be 1998 tiles AND tileable. So I'd actually solve your ironically-mentioned challenge:
A more realistic estimate of 18x115 is 2070, which is still much better than where we started in this thread.siggboy wrote:Probably steel furnace designs is not something you should overthink or make a science. But we'll all be surprised when dragontamer dazzles us with his 2000 square tile design for 3 belts
Re: Steel Furnace setup: 3-express belts of output
Here are a couple more concepts if you want to be more compact at the expense of spending massively more resources, and not using underground belt braiding (i.e. express belts only)
Pretty straightforward way to shave 1 tile off the diminisions for an entire express belt of input or output:
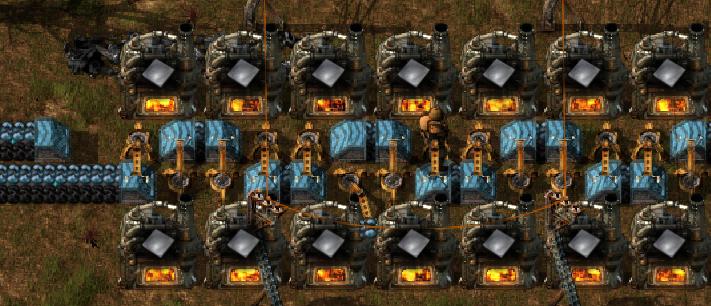
For output this assumes you only use 1 lane of each belt - it's incredibly wasteful in terms of underground express belts, but it's more compact. It's difficult to use this on both sides of the furnaces for power supply reasons but can still shave a tile off of any design which uses a single express belt between two rows of inserters and has space for medium power poles on the far side of the furnaces, it's basically a trivial if expensive space-optimization.
And the "honest belt braiding" technique which allows packing 3 belts into 2 tiles:
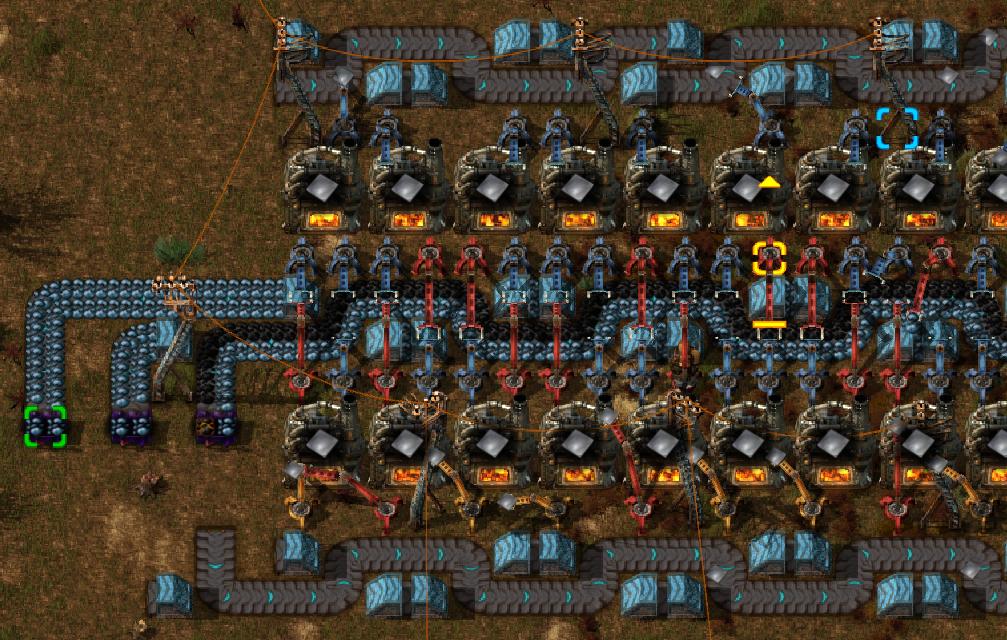
That would let you make a longer design, as it allows packing 5 lanes of ore into the gap between two furnace rows (although realistically you might only be able to use 4 lanes of ore due to belt-balancing difficulties - although this could be solved with a rainbow belt setup which mixes all the belts). It should also allow taking away about 5.8 lanes of plates (it's hard to compress the "weaved" lane). The major nuisance of this layout is you need to carefully balance the inserters and also the benefit is mainly in being longer, which is also kind of a nuisance since there comes a point where a layout is too long to be really practical.
Sorry I couldn't be bothered forming either into real setups, especially as I'm mainly interested in cheap, compact and straightforward to build.
Pretty straightforward way to shave 1 tile off the diminisions for an entire express belt of input or output:
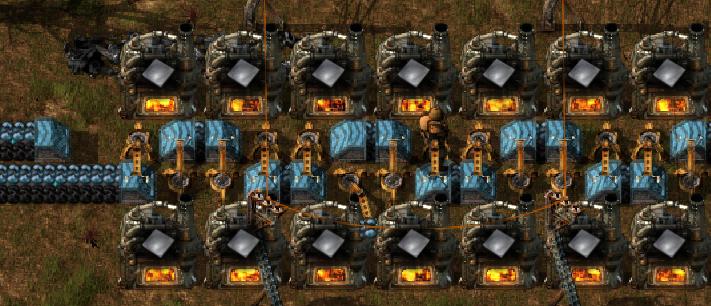
For output this assumes you only use 1 lane of each belt - it's incredibly wasteful in terms of underground express belts, but it's more compact. It's difficult to use this on both sides of the furnaces for power supply reasons but can still shave a tile off of any design which uses a single express belt between two rows of inserters and has space for medium power poles on the far side of the furnaces, it's basically a trivial if expensive space-optimization.
And the "honest belt braiding" technique which allows packing 3 belts into 2 tiles:
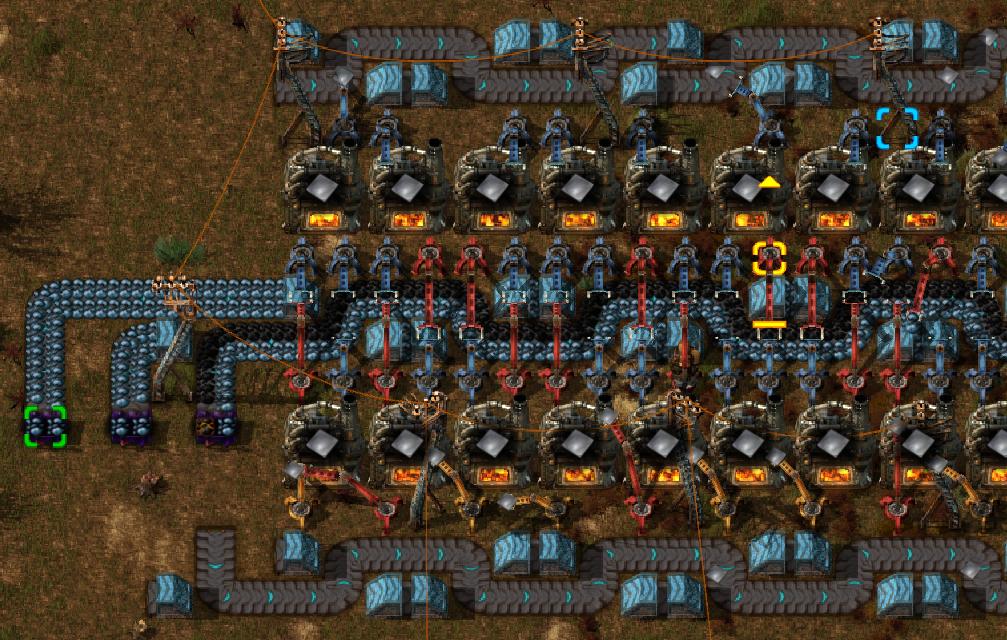
That would let you make a longer design, as it allows packing 5 lanes of ore into the gap between two furnace rows (although realistically you might only be able to use 4 lanes of ore due to belt-balancing difficulties - although this could be solved with a rainbow belt setup which mixes all the belts). It should also allow taking away about 5.8 lanes of plates (it's hard to compress the "weaved" lane). The major nuisance of this layout is you need to carefully balance the inserters and also the benefit is mainly in being longer, which is also kind of a nuisance since there comes a point where a layout is too long to be really practical.
Sorry I couldn't be bothered forming either into real setups, especially as I'm mainly interested in cheap, compact and straightforward to build.
-
- Fast Inserter
- Posts: 154
- Joined: Fri Jul 15, 2016 1:44 am
- Contact:
Re: Steel Furnace setup: 3-express belts of output
Hmm, BlakeMW's post gives me an idea of the fundamentals at play here. (As usual, my idea of fundamentals is constantly changing. Ah well...)
Assuming 3-belts of output, 210 steel furnaces are a must, as are 420 inserters (210 input, 210 output). So we have a 2x2, and two 1x1 inserters to "tile". By "combing", I think I've reached the absolute amount of compression to be had here (each furnace block uses the bare minimum: for a 6-tiles of use per inserter/furnace). The "Z" pattern, or putting input on one side and output from the "other" side innately leads to 1 or 2-tiles of "waste" (which has typically be used to place power-poles). Instead, I shove power-poles into the lanes themselves and use underground belts to get around the poles for the "comb" design.
After that, we have 6-lanes of Iron Ore as input as an absolute necessity. (120 Ore/second). And 6-lanes of Iron Plates as output. A design that has not been explored is a "conversion", where as Iron Ore is consumed, the spare room is turned into Iron Plates. Some really crazy-rainbow belt strategy could accomplish this (probably will all of the inserters wired to "pulse" plus some memory circuits so that you can keep a precise count of everything on the belts).
I think a hybrid of BlakeMW's original Rainbow belt solution plus my "Combing" solution (without the combing however: just the long inserter + yellow inserter for the efficient 2x3 footprint) would offer 95% of an output belt, and is probably the "best" solution as long as you're fine with a 95% output belt. A funny idea would be to use rocket-fuel in BlakeMW's original Rainbow Belt solution probably pushes efficiency to ~99%.
Assuming 3-belts of output, 210 steel furnaces are a must, as are 420 inserters (210 input, 210 output). So we have a 2x2, and two 1x1 inserters to "tile". By "combing", I think I've reached the absolute amount of compression to be had here (each furnace block uses the bare minimum: for a 6-tiles of use per inserter/furnace). The "Z" pattern, or putting input on one side and output from the "other" side innately leads to 1 or 2-tiles of "waste" (which has typically be used to place power-poles). Instead, I shove power-poles into the lanes themselves and use underground belts to get around the poles for the "comb" design.
After that, we have 6-lanes of Iron Ore as input as an absolute necessity. (120 Ore/second). And 6-lanes of Iron Plates as output. A design that has not been explored is a "conversion", where as Iron Ore is consumed, the spare room is turned into Iron Plates. Some really crazy-rainbow belt strategy could accomplish this (probably will all of the inserters wired to "pulse" plus some memory circuits so that you can keep a precise count of everything on the belts).
I think a hybrid of BlakeMW's original Rainbow belt solution plus my "Combing" solution (without the combing however: just the long inserter + yellow inserter for the efficient 2x3 footprint) would offer 95% of an output belt, and is probably the "best" solution as long as you're fine with a 95% output belt. A funny idea would be to use rocket-fuel in BlakeMW's original Rainbow Belt solution probably pushes efficiency to ~99%.
Re: Steel Furnace setup: 3-express belts of output
The only possible issue with combining combing with a rainbow belt is that long handed inserters might have trouble grabbing from an express belt, this is much more of a problem for a free-flowing belt than a setup which is allowed to fill up the belt. Probably the best solution for this is to go to fast belt about half way along, then basic belt near the end. When the items thin out and the long handed inserters start missing a lot, going down to a fast or basic belt will maintain a good item saturation. (it seems that in 0.13 with hand size bonus even slow inserters can "scoop" up items from an express belt if the items are packed densely enough, as if they miss the item they were aiming for but scoop up the one following it, but they revert to 0.12 behaviour when the items spread out. It's never as bad as in 0.12 but can definitely lower item throughput.)
Re: Steel Furnace setup: 3-express belts of output
Well, the long handed inserter can pick up from the sides of an express belt in all circumstances. That is not a problem.BlakeMW wrote:The only possible issue with combining combing with a rainbow belt is that long handed inserters might have trouble grabbing from an express belt, this is much more of a problem for a free-flowing belt than a setup which is allowed to fill up the belt.
The problem is picking up from the sides of an express UNDERGROUND belt -- that only works if the belt is compressed enough. Even Fast Inserters have a problem with that.
That's the limiting factor in these kinds of designs that need a lot of underground belt weaving shenanigans to happen; if the belt is not compressed the inserters cannot pick up items reliably, or not at all.
Is your railroad worrying you? Doctor T-Junction recommends: Smart, dynamic train deliveries with combinator Magick
-
- Fast Inserter
- Posts: 154
- Joined: Fri Jul 15, 2016 1:44 am
- Contact:
Re: Steel Furnace setup: 3-express belts of output
I think I got it now.
9x70 design. 630 tiles for fully compressed input and output per line. For a grand total of 1890 tiles if this design were to scale up to 3 output belts. (UNDER 2000 tiles!)
In the early game, you could accomplish the same with yellow-belts with 2x12 (24 total) steel furnaces (or 2x24 or 48 stone furnaces in the super early game) to fully saturate a yellow-belt's worth of iron.
9x70 design. 630 tiles for fully compressed input and output per line. For a grand total of 1890 tiles if this design were to scale up to 3 output belts. (UNDER 2000 tiles!)
In the early game, you could accomplish the same with yellow-belts with 2x12 (24 total) steel furnaces (or 2x24 or 48 stone furnaces in the super early game) to fully saturate a yellow-belt's worth of iron.
Re: Steel Furnace setup: 3-express belts of output
Wow that was indeed an easy optimization to be had here. Simply run the belts through the middle and use red inserters for the output.
Nice. I'll make a blueprint of this and post it here.
Nice. I'll make a blueprint of this and post it here.
Is your railroad worrying you? Doctor T-Junction recommends: Smart, dynamic train deliveries with combinator Magick
Re: Steel Furnace setup: 3-express belts of output
Well you've left out the input parts, which is not technically legal, since the belts don't mix themselves :).dragontamer5788 wrote:9x70 design. 630 tiles for fully compressed input and output per line. For a grand total of 1890 tiles if this design were to scale up to 3 output belts. (UNDER 2000 tiles!)
Turns out, the input needs to be only 4 tiles high (for a 9x74) footprint, if you want to have a coal belt that conveniently runs across the furnaces:
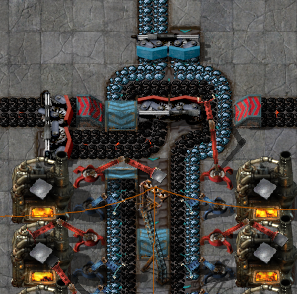
If you allow for separate coal feeds, then the column gets one tile shorter. This is then a 9x73 footprint, and probably what gheift has in store for us (657 square tiles) (gheift, sorry dude, but dragontamer figured it all out, you can now dispose of that screenshot that you've hashed :):
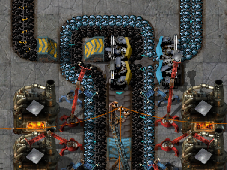
I'm still a bit amused that the only change from my initial post was reverting the output direction towards the middle column. The simplest ideas are often the best, so well done, dragontamer; probably this actually is the end of the line in terms of floor space required for coal-based smelting (it's only ~10% bigger than an equivalent e-furnace setup with full beacon coverage, however that's not counting the effect from PM3).
blueprint
Is your railroad worrying you? Doctor T-Junction recommends: Smart, dynamic train deliveries with combinator Magick
-
- Fast Inserter
- Posts: 154
- Joined: Fri Jul 15, 2016 1:44 am
- Contact:
Re: Steel Furnace setup: 3-express belts of output
Frankly, I'm surprised it is anywhere close to competitive against an optimized beacon setup. PM3 + Speed Beacons is a huge bonus in footprint.siggboy wrote:I'm still a bit amused that the only change from my initial post was reverting the output direction towards the middle column. The simplest ideas are often the best, so well done, dragontamer; probably this actually is the end of the line in terms of floor space required for coal-based smelting (it's only ~10% bigger than an equivalent e-furnace setup with full beacon coverage, however that's not counting the effect from PM3).
Steel Furnaces have the benefit of being 2x2 instead of 3x3. But still... speed beacons are hella good. I still think the rainbow belt idea (with rocket fuel) is worth a consideration though. 70 furnaces only use 12.6MW, or approximately a rocket fuel once every 17-seconds. In fact, one rocket fuel lasts over 20-minutes. A stack of 5-rocket fuel would last 1-hour and 40 minutes.
So for all intents and purposes, a rainbow belt rocket-fuel based setup is effectively working at 40 items / second for hours at a time. Its well over 99% effective blue-belt usage (its 99.86% of a blue belt. Or 39.944 Iron Plates / second output). The "Recirculation Problem" still needs to be addressed, but an overall-factory design (ie: all furnaces share a recirculate belt) would somewhat fix that.
Re: Steel Furnace setup: 3-express belts of output
Well, Blake has already shown a solution with a rainbow belt that gives you 100% compressed plates at the output (without having to use more than 70 furnaces).
But even if you use the naive solution that uses a small percentage of the belt for coal it would still be good enough. Using rocket fuel would make it almost perfect (as you've pointed out). There might be a problem though due to latency of the rocket fuel reaching the furnaces (unless the game keeps at least 1 fuel buffered in the furnace, then that wouldn't be a problem I guess).
Regarding the space efficiency of e-beacons: I think you underestimate the space that is needed for an energy efficient layout. Each Beacon uses 9 square tiles, and the furnace as well. If you sandwich the furnaces, then you need 18 square tiles per furnace (2 * 4.5 for the beacons and 9 for the furnace proper), and they'll have a crafting speed of 9.4. You also need 12 square tiles for the input/output.
A steel furnace needs 4 square tiles and 5 square tiles for the input/output, for a total of 9.
So we have 30 square tiles at a speed of 9.4 (3.19 square tiles per cycle) vs. 9 square tiles at a speed of 2 (4.5 square tiles per cycle).
However, there is overhead at the margins of the e-furnace setup, and the output side is not as neat either. On the other hand, the above calculation does not take into account the effect from PM3 (+20% per cycle), if you assume that those PM3 have actually amortized their cost (which takes a long time).
If you count the footprint of an actual setup and normalize it to 1 belt of output you get about 485 square tiles (vs. 657 for the steel furnaces). That's ~35% smaller, but it does assume PM3 in the furnaces and that the e-setup actually tiles perfectly, which is not the case.
Also, the e-furnaces use up a lot more energy per plate, and there's a huge upfront cost for making the modules (not only the PM3, also the SM3 for the beacons).
If you take all that into account, and convert it into "footprint" somehow, the e-furnaces suddenly don't look as sexy any longer. With the inserter stack size mess it has become a lot harder to make a useful "smart furnace" array, and those were the prime candidates for actually using e-furnaces.
Turning ore into plates in bulk is a lot more efficient with steel furnaces (it's easier to mine the coal required compared to build the energy for the electric furnaces).
Here's a setup for e-furnace, maybe you want to optimize it:
But even if you use the naive solution that uses a small percentage of the belt for coal it would still be good enough. Using rocket fuel would make it almost perfect (as you've pointed out). There might be a problem though due to latency of the rocket fuel reaching the furnaces (unless the game keeps at least 1 fuel buffered in the furnace, then that wouldn't be a problem I guess).
Regarding the space efficiency of e-beacons: I think you underestimate the space that is needed for an energy efficient layout. Each Beacon uses 9 square tiles, and the furnace as well. If you sandwich the furnaces, then you need 18 square tiles per furnace (2 * 4.5 for the beacons and 9 for the furnace proper), and they'll have a crafting speed of 9.4. You also need 12 square tiles for the input/output.
A steel furnace needs 4 square tiles and 5 square tiles for the input/output, for a total of 9.
So we have 30 square tiles at a speed of 9.4 (3.19 square tiles per cycle) vs. 9 square tiles at a speed of 2 (4.5 square tiles per cycle).
However, there is overhead at the margins of the e-furnace setup, and the output side is not as neat either. On the other hand, the above calculation does not take into account the effect from PM3 (+20% per cycle), if you assume that those PM3 have actually amortized their cost (which takes a long time).
If you count the footprint of an actual setup and normalize it to 1 belt of output you get about 485 square tiles (vs. 657 for the steel furnaces). That's ~35% smaller, but it does assume PM3 in the furnaces and that the e-setup actually tiles perfectly, which is not the case.
Also, the e-furnaces use up a lot more energy per plate, and there's a huge upfront cost for making the modules (not only the PM3, also the SM3 for the beacons).
If you take all that into account, and convert it into "footprint" somehow, the e-furnaces suddenly don't look as sexy any longer. With the inserter stack size mess it has become a lot harder to make a useful "smart furnace" array, and those were the prime candidates for actually using e-furnaces.
Turning ore into plates in bulk is a lot more efficient with steel furnaces (it's easier to mine the coal required compared to build the energy for the electric furnaces).
Here's a setup for e-furnace, maybe you want to optimize it:
Is your railroad worrying you? Doctor T-Junction recommends: Smart, dynamic train deliveries with combinator Magick
Re: Steel Furnace setup: 3-express belts of output
This is to gheift: I look at your design and I cannot figure out which is the coal line nor how it's put into the furnaces.
Re: Steel Furnace setup: 3-express belts of output
I actually came up with a solution for the "Recirculation Problem" which doesn't require recirculation.dragontamer5788 wrote: The "Recirculation Problem" still needs to be addressed, but an overall-factory design (ie: all furnaces share a recirculate belt) would somewhat fix that.
Basically you calculate the exact ratio of Ore:Coal required, for example 8000kJ:315kJ or 1600:63, that is 63 coal for every 1600 ore. You prime the furnaces with coal (which can be done automatically), then instead of feeding the correct ratio of ore: coal, instead you feed a slightly fuel-rich mixture to the furnaces, for example instead of using 1600:63, you use 1600:64 (which happens to be exactly 96% ore).
By using a coal rich mixture you basically guarantee that if an item type accumulates at the end of a belt, it will be coal, you also guarantee the furnace's fuel buffers will be kept topped up. When coal is accumulating at the end of the belt you remove it using a filter inserter (I use a circuit condition, along the lines of "Coal > Ore": this means if everything is accumulating due to backlogging it doesn't remove the coal), you then need to dispose of that coal in some manner.
The nice thing is, that it's very predictable. The input is 1600 Ore: 64 Coal, the output is 1600 Plates: 1 Coal, because fuel is being outputted at a predictable ratio you can also guarantee its elimination, for example if the iron plates are being taken away by train, then it is quite probable that at least 1 coal will need to be burned to deliver the 1600 plates. You could also put it in an active provider chest, or add it to a fuel belt with priority over the fuel already on the belt.
Note that while in the above I assume a fuel-rich mixture, you could also do an ore-rich mixture, if for some reason it's more favorable to send a few pieces of ore onwards. The point is by using a slightly biased ratio you only need to worry about disposal of the richer fraction of the mixed belt because consumption of the lean fraction is guaranteed.
Re: Steel Furnace setup: 3-express belts of output
The coal and ore are put on mixed belts (one belt lane for each), and fed down at the outside of the furnace column. The output is done towards the center.bripi wrote:This is to gheift: I look at your design and I cannot figure out which is the coal line nor how it's put into the furnaces.
There is no single "coal line", the outer belts share one lane for coal and one lane for ore.
Is your railroad worrying you? Doctor T-Junction recommends: Smart, dynamic train deliveries with combinator Magick
-
- Fast Inserter
- Posts: 154
- Joined: Fri Jul 15, 2016 1:44 am
- Contact:
Re: Steel Furnace setup: 3-express belts of output
I haven't seen anybody really talk about bots, so here's my solution for bot layout. 25 for the first two furnaces, then 16 tiles for each additional furnace. You'll also need a roboport (4x4 tiles) every now and then, but I'm really only demonstrating the basics of this.
70 furnaces will take up 569 tiles (plus the occasional roboport for 16 every 25x25 or 625 tiles or so). Bonus points: I use 4-furnaces per requester / provider chest and only use medium poles.
Note: the above picture demonstrates the concept. In practice, the setup looks like this:
The concept is to extend "diagonally", but build out horizontally / vertically if you like. This setup effectively extends diagonally at 8-tiles per furnace.
-------------
The "obvious" setup is the following, which is probably the most compact. However, this layout uses double the chests than the other layout.
In hindsight, I could "fill" those spots where the substations are with a few more steel furnace setups. With a bit more optimization, I guess this "obvious" setup is more dense, but it uses far more chests. Use this layout if you want the absolute minimum space I guess, although the "diagonal" design uses only 12.5% more space but HALF the chests. I think I'd prefer the cheaper solution? (we're using steel furnaces after all)
224 tiles used per "substation block", with 32 furnaces per substation block (the above picture only has 28 furnaces per substation block). So... that's 7-tiles per furnaces which is probably as good as you can get.
70 furnaces will take up 569 tiles (plus the occasional roboport for 16 every 25x25 or 625 tiles or so). Bonus points: I use 4-furnaces per requester / provider chest and only use medium poles.
Note: the above picture demonstrates the concept. In practice, the setup looks like this:
The concept is to extend "diagonally", but build out horizontally / vertically if you like. This setup effectively extends diagonally at 8-tiles per furnace.
-------------
The "obvious" setup is the following, which is probably the most compact. However, this layout uses double the chests than the other layout.
In hindsight, I could "fill" those spots where the substations are with a few more steel furnace setups. With a bit more optimization, I guess this "obvious" setup is more dense, but it uses far more chests. Use this layout if you want the absolute minimum space I guess, although the "diagonal" design uses only 12.5% more space but HALF the chests. I think I'd prefer the cheaper solution? (we're using steel furnaces after all)
224 tiles used per "substation block", with 32 furnaces per substation block (the above picture only has 28 furnaces per substation block). So... that's 7-tiles per furnaces which is probably as good as you can get.
-
- Fast Inserter
- Posts: 154
- Joined: Fri Jul 15, 2016 1:44 am
- Contact:
Re: Steel Furnace setup: 3-express belts of output
I actually just mapped out a design that should be 16-tiles for the first two furnaces (4x4), and 15-tiles for each additional furnace. For a scaling of 7.5 tiles per furnace. ("Diagonal" based, with only one provider chest and one requester chest every four furnaces)
Still not as dense as the straightforward design with substations (7-tiles per furnace), but with half the chests I'm feeling pretty confident. Apparently, playing around with the exact placement of the steel furnacese with respect to the chests may result in severe changes to the design sizes. Very interesting... I'll play around with it and see if I can get it even smaller.
Still not as dense as the straightforward design with substations (7-tiles per furnace), but with half the chests I'm feeling pretty confident. Apparently, playing around with the exact placement of the steel furnacese with respect to the chests may result in severe changes to the design sizes. Very interesting... I'll play around with it and see if I can get it even smaller.
Re: Steel Furnace setup: 3-express belts of output
It takes 44*15 = 660 tiles (or 1980 tiled 3 times). However that isn't really an apples to apples to comparison as the 44*15 includes 3 tiles width at front and back for mixing which I don't think the other furnaces include in their counts. Removing that takes the solution down to 38*15 = 570 tiles (1710 for 3 belts). The return lane also isn't that heavily used and might be sharable across more than one tiled instance, but you have to be careful how it is mixed back in or I assume it will further skew the fuel mixture.
Re: Steel Furnace setup: 3-express belts of output
I'm still pretty new to the game, but I always had a feeling that steel furnaces were better. This is the steel furnace setup that I use. I just remove the coal line off the back and extend by adding more furnaces.
- Attachments
-
- Capture.PNG (899.51 KiB) Viewed 11074 times