That's due to directional biases, water prefers to flow more in some directions than others which can cause the flow from one offshore pump to block the flow from another by completely filling the pipe before the other offshore pump has the chance to add water. It happens because factorio does not have a realistic pressure model. I'll try and give a graphic example:Patric20878 wrote:Well that's bad. If placement order affects this, why doesn't replacing offshore pumps and pipes make them split more evenly?
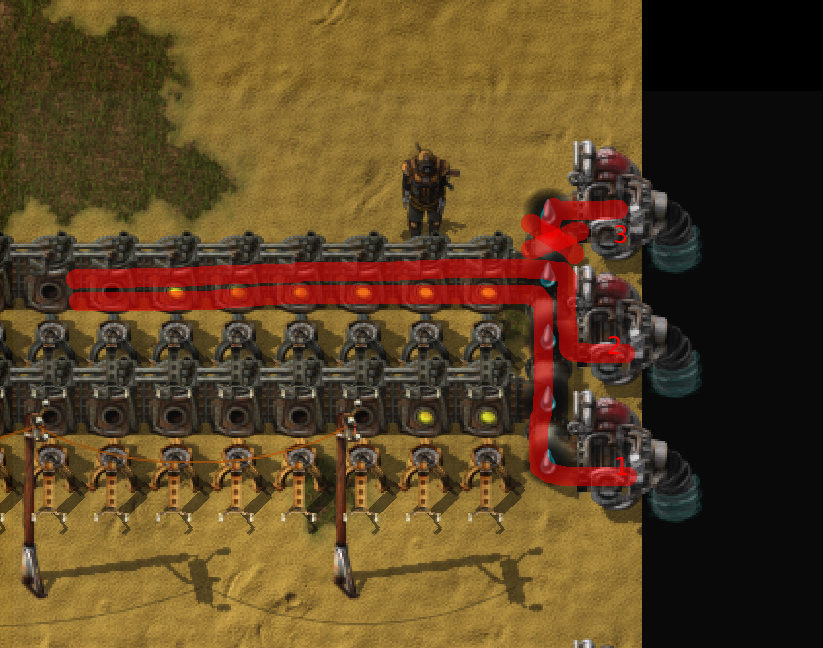
Water from pump 1 wants to go up.
Water from pump 2 also wants to go up.
Once pump3 gets its turn, its water can't get to the bottom boiler string, because the up-biased water from pump 1 and 2 has blocked it. Result: Pump3 is underutilized and the bottom boiler string is starved.
The directional biases here dominate over placement order bias.
That's not a perfect description of what happens, but I think something like that does happen. Remember: Not a pressure model. Don't expect it to act like water.
Btw something else is that small pumps can do some seriously weird things. I have setups which definitely show small pumps causing water to teleport ahead - actually skipping a bunch of pipe segments then backfilling. This behavior is highly directional (i.e. tends to happen only in certain directions) and it's difficult to explain, except as some weird hack to make small pumps work "better". I haven't come up with setups which definitely show small pumps causing problems, but I wouldn't be surprised if small pumps in some cases allow water to skip over boilers and not get heated. It may also be a similar phenomena to offshore pumps in empty systems, where the water seems to rapidly flow to the end of the system, too rapidly for the boilers to heat it properly. Small pumps are always fine after boilers though (although of dubious usefulness except as valves).