Let's see your clever builds
-
- Manual Inserter
- Posts: 4
- Joined: Thu Apr 14, 2016 2:47 am
- Contact:
Re: Let's see your clever builds
I have been playing with the idea of using a cargo train as a long filtered chest for a while. This I tried this out and it works very well. it could actually support one more advanced circuit factory if I could fit it.
Re: Let's see your clever builds
You can fit a lot more than that. viewtopic.php?p=37082#p37082
-
- Manual Inserter
- Posts: 4
- Joined: Thu Apr 14, 2016 2:47 am
- Contact:
Re: Let's see your clever builds
I did not even think about long handed inserters that would expand it in size but could mean I could push out more. Thanks for pointing to that!DaveMcW wrote:You can fit a lot more than that. viewtopic.php?p=37082#p37082
Re: Let's see your clever builds
EDIT: As of version 0.13, which came out 2 months after I made this post, accumulators can be connected directly to circuit networks to read the amount of energy. Thankfully this has completely obsoleted the tedious design detailed in this post. Now all you have to do is wire a single accumulator to the control pumps, set them to turn on when A < 10, and make sure the pumps can get power, such as from a small isolated solar / accumulator network.
This is my version of the steam engine backup. The point is to make the steam engines turn on when power diminishes for any reason, such as accumulators expiring or laser turrets activating. But if accumulators are sufficient, it won't turn on.
Note that there are two isolated electrical systems here. The power for the backup system, is the 3 solar panels and 3 accumulators. It should be enough to power the 3 pumps and the combinators continuously.
The lamp is a visual indicator when the engines turn on.
Description:
I wanted it to be fast enough, and then stay on long enough, to support many laser turrets without hesitation or interruption. The goal then was to make it as sensitive and responsive as possible, so I devised a trigger mechanism involving fluid levels and a pump to determine when power drops even slightly below demand. I measured the total activation delay as 0.20 seconds (by measuring pixels on the power graph). It will work without any combinators, but then it will only stay on for a few seconds, then briefly turn off and back on. It does this because the steam engines provide the necessary power. (Once turned on, it's not possible to tell if and when the network 'would' have enough power if the engines were off.) The slight turn-off, though brief, might be enough to affect laser turrets in a battle, which is bad because the fights are fast and furious in this game. It's sub-optimal.
So, the goal of the circuit is to configure a delay such that, once the backup is triggered, it won't turn off until at least a configurable amount of time has passed. This might have been done before, but I devised this one myself.
All five deciders have A, 1 as output.
Three deciders act as NOR logic gates, parameter A=0. (The cross-coupled ones constitute a NOR latch.)
Bottom center constant is output 1 on B.
Bottom right arithmetic is A * B, output on B.
Bottom left is B < (time)
Pumps for primary backup, and lamp, are A > 0
Bottom left decider is the minimum duration of the backup run. 1800/60 = 30 seconds. Or you could make it 300 for 5 seconds, 900 for 15 seconds, whatever.
Top left is the trigger. The more precisely tuned this is, the faster the trigger. I filled one tank, severed the adjacent pipe, then attached the other tank, the pump, and the pipe above the pump. Hopefully this will let you get exactly 2500 water in the system, a repeatable process. The trigger is attached to the 'fuller' tank, and for me the perfect setting is Water < 1308. If I set it to 1309, the backup activates unnecessarily. But at 1308, I have never once seen it turn on by a jitter or rounding error.
I don't know if this is the kind of thing this thread is for, if not let me know.
String mod: viewtopic.php?t=6742
Blueprint string (for compact combinator & panel portion, including wires and settings):
This is my version of the steam engine backup. The point is to make the steam engines turn on when power diminishes for any reason, such as accumulators expiring or laser turrets activating. But if accumulators are sufficient, it won't turn on.
Note that there are two isolated electrical systems here. The power for the backup system, is the 3 solar panels and 3 accumulators. It should be enough to power the 3 pumps and the combinators continuously.
The lamp is a visual indicator when the engines turn on.
Image 1
Zoom in for clearer wires:
Image 2
Detail for sensor:
Image 3
Instructions: Blueprint string for the more compact version is below. String mod is linked below. (EDIT: It looks like blueprint strings just aren't precise enough to handle this, so, the string doesn't really work. Sorry about that. But the wiring is visible, and the combinator settings are detailed below, so you can reconstruct it.) Connect the medium pole to the (fuller) tank via green wire. Connect the lamp, or the output connected to the lamp, to the 3 hot water pumps at the steam engines via green wire. (Note: these two green wires can be combined.) (EDIT: You really only need two pumps to fully power a row of 10 engines, not 3. See the new image at the bottom.) Set pumps to A > 0. Configure delay via bottom-left combinator (unit 1/60 second), sensitivity via top-left. (For me sensitivity is 1308, using repeatable method below.) You can use a lamp with a decider to measure the level in the tank. Also make sure the pumps to the engines can be powered by the same 3 solar panels which power the system. The sole pump at the trigger mechanism tanks must only be powered by the main grid. Keep this backup system isolated from the main grid, or it will drain the 3 accumulators.Description:
I wanted it to be fast enough, and then stay on long enough, to support many laser turrets without hesitation or interruption. The goal then was to make it as sensitive and responsive as possible, so I devised a trigger mechanism involving fluid levels and a pump to determine when power drops even slightly below demand. I measured the total activation delay as 0.20 seconds (by measuring pixels on the power graph). It will work without any combinators, but then it will only stay on for a few seconds, then briefly turn off and back on. It does this because the steam engines provide the necessary power. (Once turned on, it's not possible to tell if and when the network 'would' have enough power if the engines were off.) The slight turn-off, though brief, might be enough to affect laser turrets in a battle, which is bad because the fights are fast and furious in this game. It's sub-optimal.
So, the goal of the circuit is to configure a delay such that, once the backup is triggered, it won't turn off until at least a configurable amount of time has passed. This might have been done before, but I devised this one myself.
All five deciders have A, 1 as output.
Three deciders act as NOR logic gates, parameter A=0. (The cross-coupled ones constitute a NOR latch.)
Bottom center constant is output 1 on B.
Bottom right arithmetic is A * B, output on B.
Bottom left is B < (time)
Pumps for primary backup, and lamp, are A > 0
Bottom left decider is the minimum duration of the backup run. 1800/60 = 30 seconds. Or you could make it 300 for 5 seconds, 900 for 15 seconds, whatever.
Top left is the trigger. The more precisely tuned this is, the faster the trigger. I filled one tank, severed the adjacent pipe, then attached the other tank, the pump, and the pipe above the pump. Hopefully this will let you get exactly 2500 water in the system, a repeatable process. The trigger is attached to the 'fuller' tank, and for me the perfect setting is Water < 1308. If I set it to 1309, the backup activates unnecessarily. But at 1308, I have never once seen it turn on by a jitter or rounding error.
I don't know if this is the kind of thing this thread is for, if not let me know.
String mod: viewtopic.php?t=6742
Blueprint string (for compact combinator & panel portion, including wires and settings):
Blueprint string, defective
The proper way to use the engine pumps
Last edited by Aru on Sun Feb 12, 2017 4:38 pm, edited 17 times in total.
Designs: v0.16 | Automated nuclear | Centrifuge ratios | Solar + Accumulator
-
- Burner Inserter
- Posts: 9
- Joined: Sun Apr 17, 2016 12:33 pm
- Contact:
Re: Let's see your clever builds
This is how I do it:
One Extra basic efficiency module assembly for the drills.
One Extra basic efficiency module assembly for the drills.
- Attachments
-
- Modules and Destructor's
- Factorio module and destructor build.jpg (509.24 KiB) Viewed 16668 times
Re: Let's see your clever builds
Don't know if this really clever.
Some oil refinery with storage area and tank level indicator.
Some oil refinery with storage area and tank level indicator.
- Attachments
-
- Oil Refinery.png (4 MiB) Viewed 16634 times
Re: Let's see your clever builds
I could also show my monolithic research block, but I'm not sure giving that up is in the spirit of the game. It overproduces yellow belts and inserters (which are nice to grab to accelerate manual production of higher belts and inserters). And it is primed for overproduction of batteries, all you need to do is add three more battery plants for 5 total. (If you added a second sulfur plant it could theoretically go to 10 battery plants.) It takes as inputs: coal, petroleum, 2 balanced yellow belts of iron, 2 balanced yellow belts of copper. If the iron/copper belts aren't saturated, I don't collect too many excess items or I might not get any research done. After all, I've experiments to run, there is research to be done. But you can emulate an isolated smart inserter + smart chest network by locking out chest slots and adding 1 item to each slot. Then, you don't collect more than say, 250 belts and 100 inserters.
(It's finely tuned for 1 set of science packs per 2 seconds, but it's not thoroughly tested. It's designed for a somewhat minimal material, technology and power cost (very approximately 10 MW maximum), no modules are required, and there are no beacons. Productivity modules for the purple pack assembler when I can. It has 16 science labs, which has the 30 second projects in mind and no need for lab efficiency upgrades. They should be renamed to lab speed anyway.)
(It's finely tuned for 1 set of science packs per 2 seconds, but it's not thoroughly tested. It's designed for a somewhat minimal material, technology and power cost (very approximately 10 MW maximum), no modules are required, and there are no beacons. Productivity modules for the purple pack assembler when I can. It has 16 science labs, which has the 30 second projects in mind and no need for lab efficiency upgrades. They should be renamed to lab speed anyway.)
Designs: v0.16 | Automated nuclear | Centrifuge ratios | Solar + Accumulator
Re: Let's see your clever builds
I like things to be narrow and needed to make something for Green Science Production. I created this expandable production line for regular belts and regular inserters.
I recently saw how one can utilize underground belts near inserters. In the image, I'm routing my belts under the assembers and having inserters pick directly from where the underground belt surfaces. For the inputs, the green circuits (green line) are on the left side as only the Inserter production requires it. The gears and iron (grey lines) are used for both productions. I'm taking advantage that inserters will place items on the far side, (in this case the inserter is placed on the right side of the belt). The belt is always placed on the left side. The output goes directly to Green Science Production. Makes for a narrow production line, but the downside is that it can get tall. So far this hasn't been an issue.
I recently saw how one can utilize underground belts near inserters. In the image, I'm routing my belts under the assembers and having inserters pick directly from where the underground belt surfaces. For the inputs, the green circuits (green line) are on the left side as only the Inserter production requires it. The gears and iron (grey lines) are used for both productions. I'm taking advantage that inserters will place items on the far side, (in this case the inserter is placed on the right side of the belt). The belt is always placed on the left side. The output goes directly to Green Science Production. Makes for a narrow production line, but the downside is that it can get tall. So far this hasn't been an issue.
Re: Let's see your clever builds
Just finished this monster, it fits between 4 roboports.
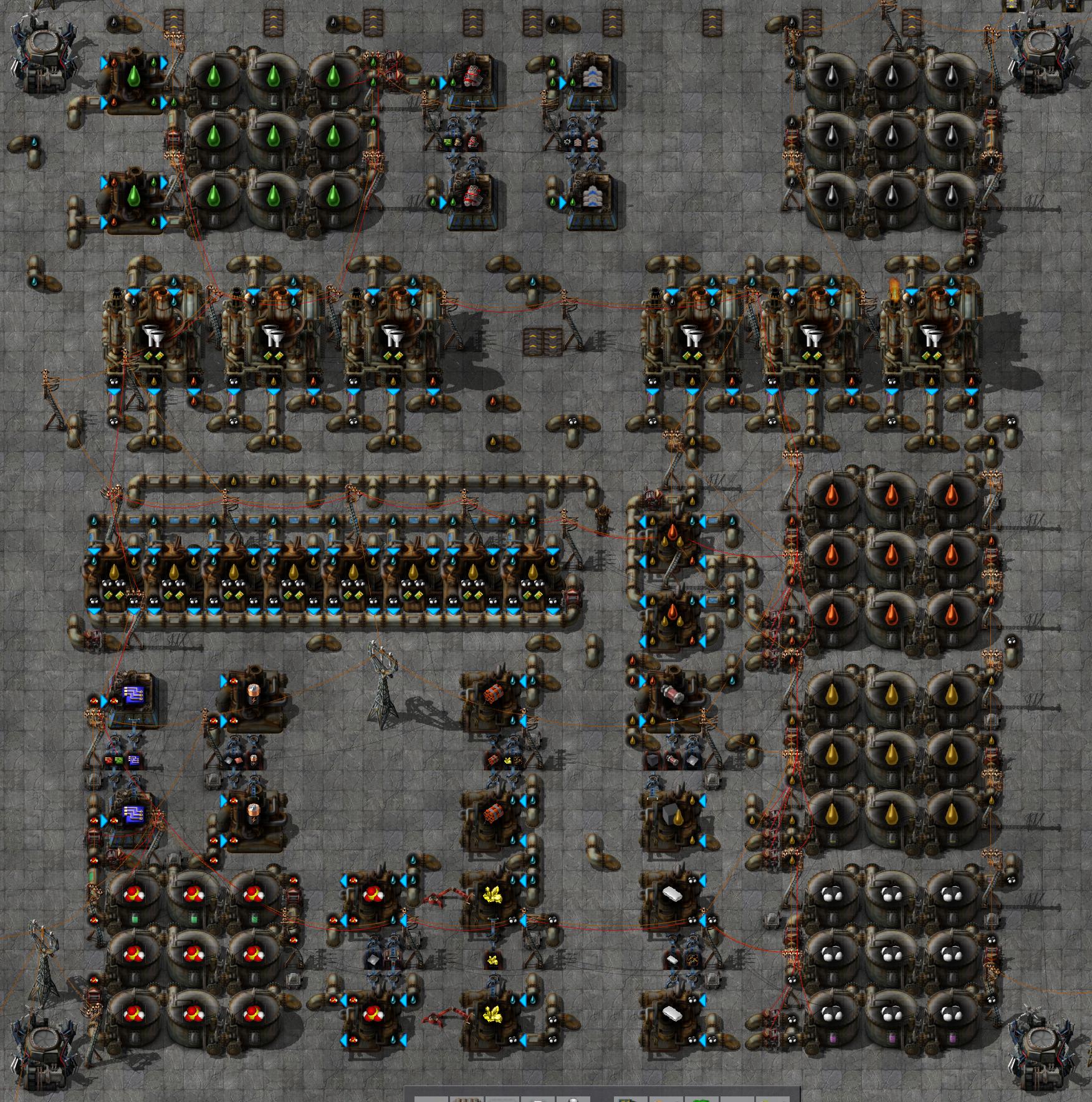
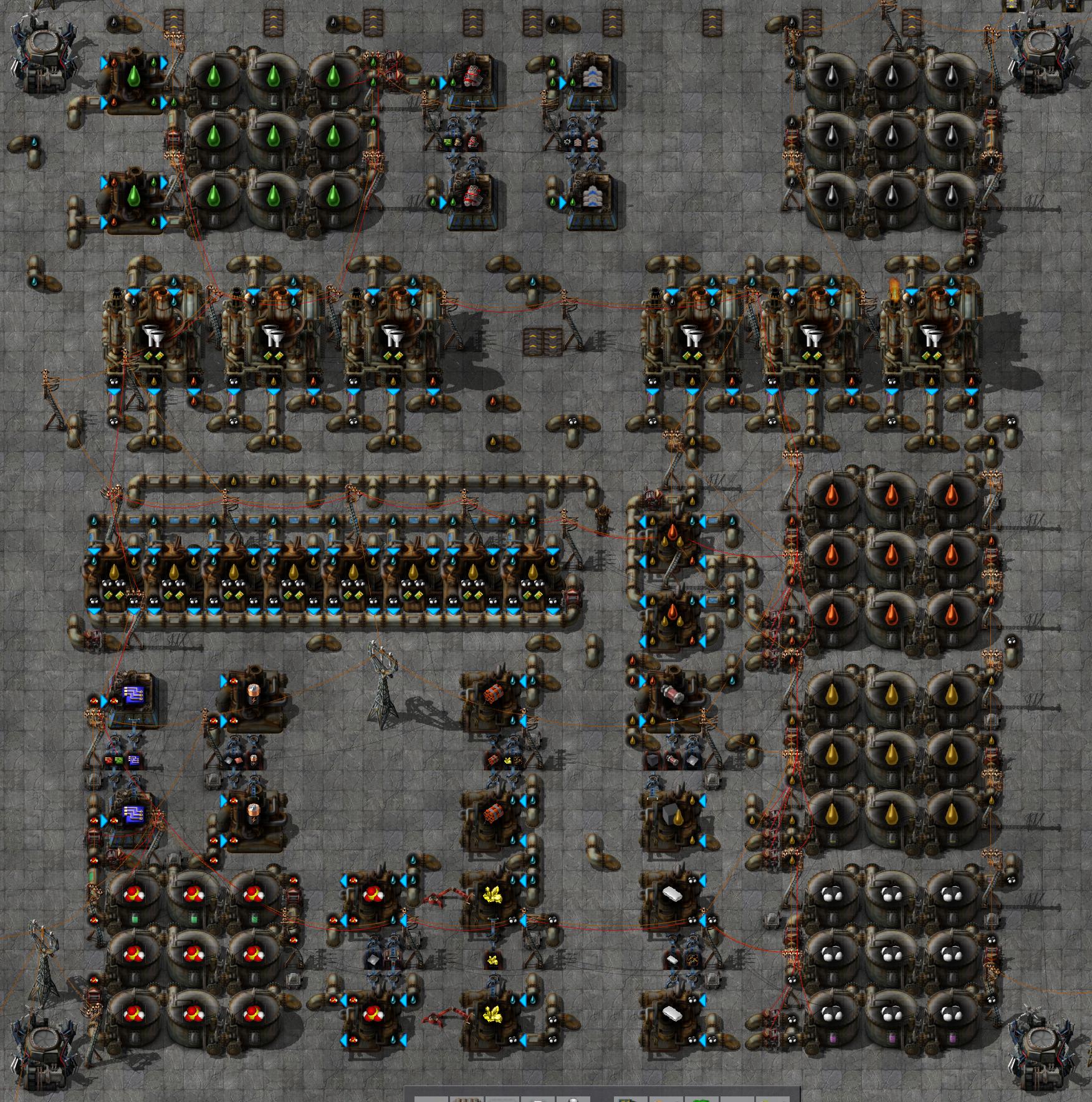
Re: Let's see your clever builds
Hey guys. First post and this is my first build (came to the forums to see what I could improve).
By the looks of what I've seen in this thread, I'm guessing I'm doing alright so far. Most of my stuff is built to be expandable with no uncontrolled overlap.
My main mines are far off site. I can't quite remember why I decided to do that.
By the looks of what I've seen in this thread, I'm guessing I'm doing alright so far. Most of my stuff is built to be expandable with no uncontrolled overlap.
My main mines are far off site. I can't quite remember why I decided to do that.
- brunzenstein
- Smart Inserter
- Posts: 1156
- Joined: Tue Mar 01, 2016 2:27 pm
- Contact:
Re: Let's see your clever builds
I don't see where you control the red wired lights and the pumps - how is this working?steinio wrote:Don't know if this really clever.
Some oil refinery with storage area and tank level indicator.
Re: Let's see your clever builds
Hello brunzenstein,
i have currently no glue about the logistic network so i tryed some stuff like putting a red wire from the tank to a lamp.
Afte selecting the lamp you get the gui shown in the picture where you can select a filter like a smart inserter.
Thus just worked fine for me.
Same by the pumps - i just put one red wire from the tank east to the pumps and select on each pump the filter.
The 4 connected tanks have all the same level, max level is 2500.
1st lamp: [item] > 624
2nd lamp: [item] > 1249
3rd lamp: [item] > 1874
4th lamp: [item] > 2498
Pump: [item] > 2495 (recognised at creating this post, could be also 2498)
Greetings steinio
i have currently no glue about the logistic network so i tryed some stuff like putting a red wire from the tank to a lamp.
Afte selecting the lamp you get the gui shown in the picture where you can select a filter like a smart inserter.
Thus just worked fine for me.
Same by the pumps - i just put one red wire from the tank east to the pumps and select on each pump the filter.
The 4 connected tanks have all the same level, max level is 2500.
1st lamp: [item] > 624
2nd lamp: [item] > 1249
3rd lamp: [item] > 1874
4th lamp: [item] > 2498
Pump: [item] > 2495 (recognised at creating this post, could be also 2498)
Greetings steinio
- Attachments
-
- red wire.png (228 KiB) Viewed 15325 times
Re: Let's see your clever builds
I've been playing with burner inserters recently. Trying to work around the coal requirement has been tricky, but I worked out a decent smelting setup. One input inserter couldn't keep up with the furnace's demands for both ore and coal, and two inserters meant that the belt couldn't keep up. I don't like the way this looks, but it works fairly well.
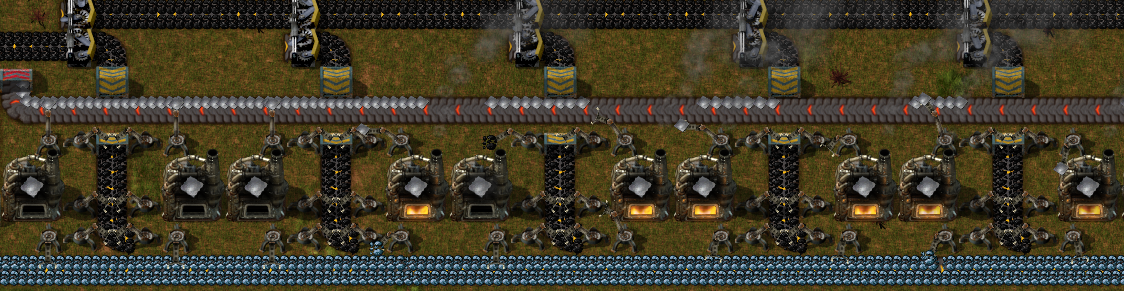
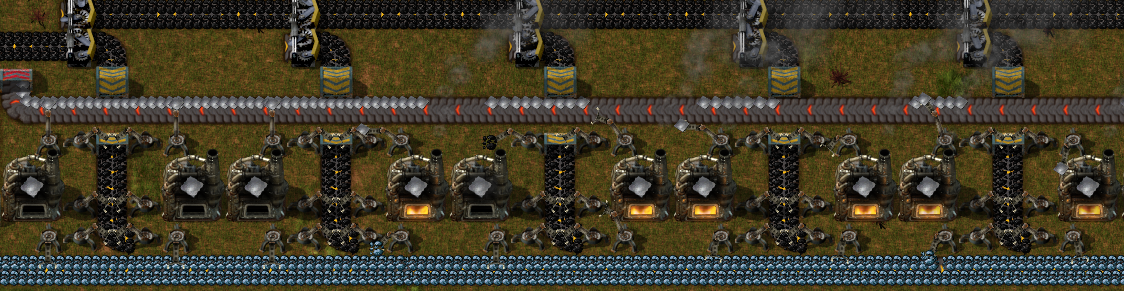
-
- Filter Inserter
- Posts: 947
- Joined: Wed Nov 25, 2015 11:44 am
- Contact:
Re: Let's see your clever builds
Why not mix the coal and ore/plate belts? It means you have less smelters per belt (since only half is for input/output), but it is also a lot more space efficient...
Re: Let's see your clever builds
Mixing the coal and ore on the same belt meant that the belt ran down too fast: burner inserters have a hard time grabbing from red belts, spending a lot of their time trying to grab an item as it goes past, and a yellow belt with half ore and half coal can only sustain ~10 furnaces (if I recall correctly from my test last night).
You say mixing the belts is more space efficient: but I would have to set up a second row to smelt the plates I need. I wonder if doing it that way is more space efficient overall?
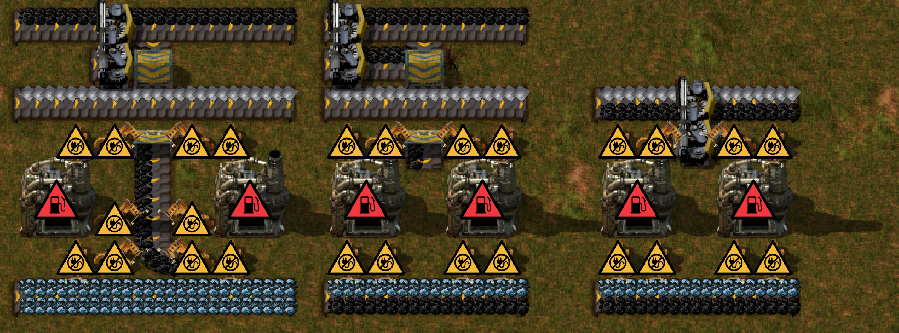
Option 1: 4/7 of the spaces along the belt are furnaces. Option 2 & 3: 4/5 of the space along the belt are furnaces. In the cross direction (normal to the flow of items); Option 1 & 2: 2/8 of the spaces are furnaces, or 1/4. Option 3: 2/6, or 1/3 of the spaces of furnaces.
Per set of two furnaces (for symmetry and simplicity here), each repeatable block has a respective area and % area of furnaces. Option 1: 7x8 = 56 spaces, 8 furnaces spaces, 8/56 = 14.2% furnaces. Option 2: 5x8 = 40 spaces, 8 furnace spaces, 8/40 = 20% furnaces. Option 3: 6x5 = 30 spaces, 8 furnaces spaces, 8/30 = 26.6% furnaces.
With Option 2 or 3, you need to set up a new line twice as often if your production of plates gets too slow. With the space I had in my factory, I needed to get more production along the same line, rather than create a second one (the location where my iron ore is coming in is not ideal). Not the best setup, as we've just seen with the math, but works nicely and doesn't require any separating materials at the end (the underground belt, just never feels or looks good to me) to get the plates by themselves again.
You say mixing the belts is more space efficient: but I would have to set up a second row to smelt the plates I need. I wonder if doing it that way is more space efficient overall?
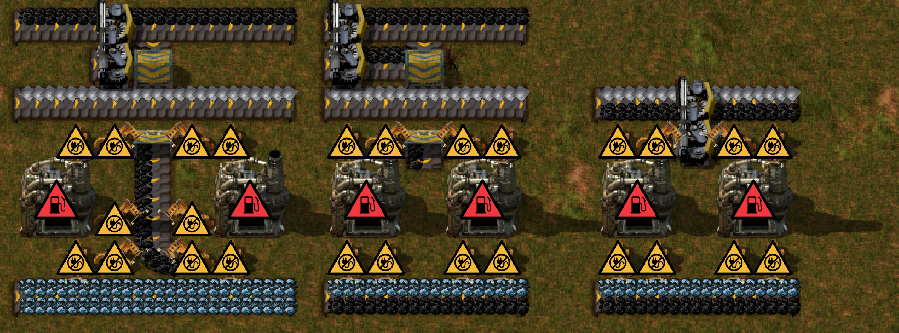
Option 1: 4/7 of the spaces along the belt are furnaces. Option 2 & 3: 4/5 of the space along the belt are furnaces. In the cross direction (normal to the flow of items); Option 1 & 2: 2/8 of the spaces are furnaces, or 1/4. Option 3: 2/6, or 1/3 of the spaces of furnaces.
Per set of two furnaces (for symmetry and simplicity here), each repeatable block has a respective area and % area of furnaces. Option 1: 7x8 = 56 spaces, 8 furnaces spaces, 8/56 = 14.2% furnaces. Option 2: 5x8 = 40 spaces, 8 furnace spaces, 8/40 = 20% furnaces. Option 3: 6x5 = 30 spaces, 8 furnaces spaces, 8/30 = 26.6% furnaces.
With Option 2 or 3, you need to set up a new line twice as often if your production of plates gets too slow. With the space I had in my factory, I needed to get more production along the same line, rather than create a second one (the location where my iron ore is coming in is not ideal). Not the best setup, as we've just seen with the math, but works nicely and doesn't require any separating materials at the end (the underground belt, just never feels or looks good to me) to get the plates by themselves again.
- brunzenstein
- Smart Inserter
- Posts: 1156
- Joined: Tue Mar 01, 2016 2:27 pm
- Contact:
Re: Let's see your clever builds
Why your not simplifying matter by using a electric furnace?joes01 wrote:Mixing the coal and ore on the same belt meant ....
Re: Let's see your clever builds
Because, you have access to steel furnaces before electric ones.brunzenstein wrote:Why your not simplifying matter by using a electric furnace?joes01 wrote:Mixing the coal and ore on the same belt meant ....
Designs: v0.16 | Automated nuclear | Centrifuge ratios | Solar + Accumulator
Re: Let's see your clever builds
I would still need the coal to feed the burner inserter itself. Changing the furnace type doesn't fully address the problem; would reduce the required actions of the loading inserters, but would not solve the issue of needing to have ore and coal on the same belt.brunzenstein wrote:Why your not simplifying matter by using a electric furnace?joes01 wrote:Mixing the coal and ore on the same belt meant ....
Re: Let's see your clever builds
btw slow inserters actually work with fast belts in the long run - once the belt clogs up, the inserter can pick from it. It will just mean that the rear furnaces will start working before the front ones, but it works in total.
-
- Filter Inserter
- Posts: 952
- Joined: Sat May 23, 2015 12:10 pm
- Contact:
Re: Let's see your clever builds
but that requires the belt to be clogged first. Which means that using a fast belt there will not have any benefit anyway.V453000 wrote:btw slow inserters actually work with fast belts in the long run - once the belt clogs up, the inserter can pick from it. It will just mean that the rear furnaces will start working before the front ones, but it works in total.