pY Raw Ores Discussion
Moderator: pyanodon
Re: pY Raw Ores Discussion
if there is a slot, just like in vanilla
-
- Filter Inserter
- Posts: 771
- Joined: Sun Jun 03, 2018 8:54 am
- Contact:
Re: pY Raw Ores Discussion
because of the way hellmod worksmxpal wrote: Fri Feb 15, 2019 5:03 pmhow does changing to 1000 plate affect anything? the ratio of plate to ore wont change by thatimmortal_sniper1 wrote: Thu Feb 14, 2019 3:55 pmtry doing the ore/plte hellmod ratios with 1000 plate at the end then scale downmxpal wrote: Thu Feb 14, 2019 3:38 pm so i have to get to at least nickel pulp 02 recipe to be worth it? smelting grade 4 or pulp 01 into molten nickel is only there for misdirection?![]()
example there is a recipe that from 100 molten makes 20 plates
if you want to make 21 plate then makeing 105 molten might register as 200 or something
when it comes to small numbers do the math on paper
and my paper said that all higher tier recipes have a gain the gap beetwen recipes also increases as you go
-
- Fast Inserter
- Posts: 170
- Joined: Thu Jan 10, 2019 3:11 pm
- Contact:
Re: pY Raw Ores Discussion
This explanation makes no sense since helmod uses fractionals for everything. But just to make sure, here's 1000 platesimmortal_sniper1 wrote: Fri Feb 15, 2019 6:32 pm because of the way hellmod works
example there is a recipe that from 100 molten makes 20 plates
if you want to make 21 plate then makeing 105 molten might register as 200 or something
when it comes to small numbers do the math on paper
and my paper said that all higher tier recipes have a gain the gap beetwen recipes also increases as you go
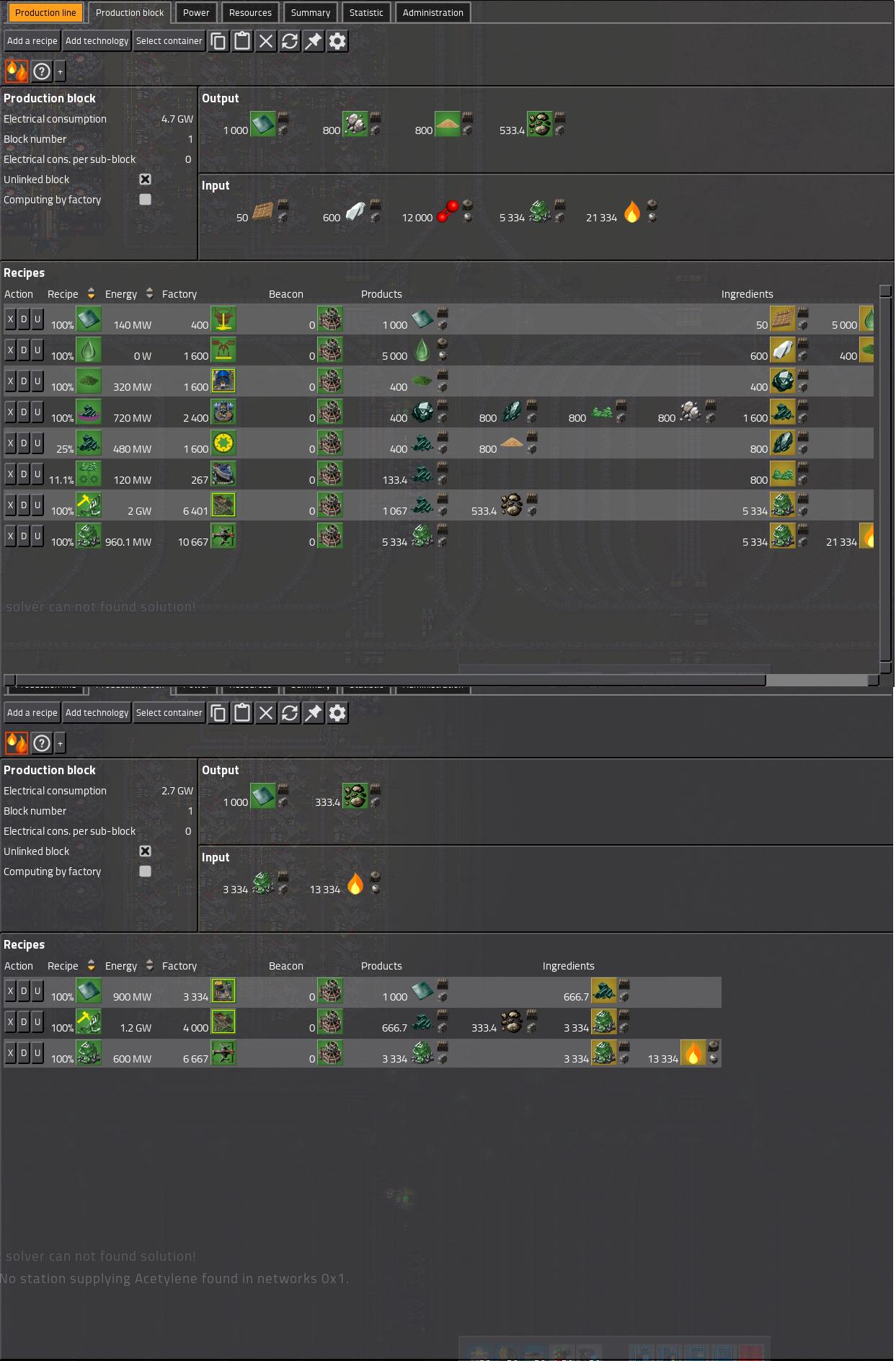
The first molten nickel recipe makes no sense to use
Re: pY Raw Ores Discussion
Was purely going of the screenshot itself. All of them make 5 plates.immortal_sniper1 wrote: Fri Feb 15, 2019 7:26 amfirst one 10:1mrbaggins wrote: Fri Feb 15, 2019 5:00 am With the higher tier nickel, that last one is close enough to the first one that adding production modules would shoot it well over (at the expense of power)
that middle one is broken though.
second 5:1 gr1 2 gr1:3 plate so 10 ore=3 plate
First one is 15.8 ore. Second is 25.2. Third is 16.7
That makes the third only 6% worse than the first.
Well crap. That shoots my theory in the foot. I'm just about to unlock modules in my py run so that's disappointinghow do you add production modules to other py machines? as far as i know only chipshooter can use production modules.
Re: pY Raw Ores Discussion
did the lead orerecipe change at some point? Or is it just really expensive? 100 acetylene is a lot, when most of the other recipes are 4 or 6 or 10 of something.
-
- Fast Inserter
- Posts: 170
- Joined: Thu Jan 10, 2019 3:11 pm
- Contact:
Re: pY Raw Ores Discussion
If you're just reading the .lua files they all look 10 times higher than they really are. It's 10 acetylene / ore (still a lot)mrbaggins wrote: Sat Feb 16, 2019 12:59 am did the lead orerecipe change at some point? Or is it just really expensive? 100 acetylene is a lot, when most of the other recipes are 4 or 6 or 10 of something.
Re: pY Raw Ores Discussion
nah, my game was actually saying 100.
However running the "redo tech" command fixed it down to 10. I'm drowning in lead now, cos I'd been building my acet so much
However running the "redo tech" command fixed it down to 10. I'm drowning in lead now, cos I'd been building my acet so much
-
- Filter Inserter
- Posts: 771
- Joined: Sun Jun 03, 2018 8:54 am
- Contact:
Re: pY Raw Ores Discussion
i did the math on paper and all recipes are progressively better
Re: pY Raw Ores Discussion
Just punched things into helmod for 4 of the nickel recipes
ore -> plate @ 10:1, 38 foundries, 25.34 nickel/s for 2.54 plate/s
ore -> G1 -> plate @ 10:2:1, 8 foundries, ~9.6 crushers, 8 nickel/s for 2.4 plate/s
ore -> G1 -> G3 -> G4 -> molten -> plate @ 40:8:2:1:12.5 molten, 1 casting unit, eats 20 nickel/s for 2.5 plate/s, but with G2 and rejects as byproducts
ore -> G1 -> G3 -> G4 -> prepared -> pulp 1 -> molten -> plate @ who knows, 1 casting unit, 12.5 nicke/s for 2.5 plate/s, a little over half the G2+rejects as the G4 recipe
something seems really suspicious there, the straight G1 recipe seems ridiculously efficient, wondering what I missed
ore -> plate @ 10:1, 38 foundries, 25.34 nickel/s for 2.54 plate/s
ore -> G1 -> plate @ 10:2:1, 8 foundries, ~9.6 crushers, 8 nickel/s for 2.4 plate/s
ore -> G1 -> G3 -> G4 -> molten -> plate @ 40:8:2:1:12.5 molten, 1 casting unit, eats 20 nickel/s for 2.5 plate/s, but with G2 and rejects as byproducts
ore -> G1 -> G3 -> G4 -> prepared -> pulp 1 -> molten -> plate @ who knows, 1 casting unit, 12.5 nicke/s for 2.5 plate/s, a little over half the G2+rejects as the G4 recipe
something seems really suspicious there, the straight G1 recipe seems ridiculously efficient, wondering what I missed
Re: pY Raw Ores Discussion
If you recylce the G2 products and the rejects the results end up being
Ore->G1->Plates (3.34 ore per plate)
Ore->G1->G3->G4->Molten->Plates (5.34 ore per plate)
Ore->G1->G3->G4->Prep Pulp->Pulp 01->Molten->Plates (3.34 ore per plate)
So yeah Probably stick with top one, not sure how the more advanced recipes compare
Ore->G1->Plates (3.34 ore per plate)
Ore->G1->G3->G4->Molten->Plates (5.34 ore per plate)
Ore->G1->G3->G4->Prep Pulp->Pulp 01->Molten->Plates (3.34 ore per plate)
So yeah Probably stick with top one, not sure how the more advanced recipes compare
Re: pY Raw Ores Discussion
i faced a crash when i try to add the recipe of tin concentrate using MIBC to helmod.
Re: pY Raw Ores Discussion
and can we please have higher tiers of automated screener? its the only extensively used building for ore processing without upgrade versions
-
- Filter Inserter
- Posts: 771
- Joined: Sun Jun 03, 2018 8:54 am
- Contact:
Re: pY Raw Ores Discussion
use modulesmxpal wrote: Mon Feb 18, 2019 6:14 pm and can we please have higher tiers of automated screener? its the only extensively used building for ore processing without upgrade versions
Re: pY Raw Ores Discussion
Hi
the higher lead tier chain is broken, when i use T1 i get 6 silver and 450 lead plates for 1000 Ore.
The Arc Furnace only produces around 80 lead plates.
And T3 gets me 7 High Grade Silver + Lead fully sintered this is 140 plates each.
This is because the Impact Crusher has a 50% chance to turn Grade 1 Lead (2plates) into Grade 2 Lead (also 2plates).
Thank you for the mod
the higher lead tier chain is broken, when i use T1 i get 6 silver and 450 lead plates for 1000 Ore.
The Arc Furnace only produces around 80 lead plates.
And T3 gets me 7 High Grade Silver + Lead fully sintered this is 140 plates each.
This is because the Impact Crusher has a 50% chance to turn Grade 1 Lead (2plates) into Grade 2 Lead (also 2plates).
Thank you for the mod
Re: pY Raw Ores Discussion
Pyanodon,
I have tried to make this mod work since the day you first released. I have been there riding one release after the next, trashing a map and restarting because the technology chains changed, dumping 100+ hour maps and restarting. The after patching joys of finding that a full ore processing or chemical chain had suddenly broken because the formulas had changed (making blueprints worthless) and requiring a full replumb to make it work. My goal was to reach the finish line without stuffing the buildings with modules in order to compensate for the deficiencies and bring this mod into full homeostasis where it would all just work. With this current map at 240 hours, I gave up and launched the rocket just to end it.
I wanted to see if this mod could stand on its own. For transparency, the few mods I kept active to run this mod was:
ChargeTransmission
DeadlockLoaders
Loader-Furnace
NoEmptyBarrels
OmegaDrill
Restack
ammo-loader
pycoalprocessing
pyfusionenergy
pyhitech
pyindustry
pyrawores
These are the trouble points that kept breaking no matter what I put into place:
Nickel
salt
methanol
Sulfur
Sufuric Acid
filtration media
biofilm
Grade 4 tin
zinc
lead
nichrome
nexelit
Vanadium
Things that just worked like a champ:
chrome production (had more chrome than a Harley Davidson national rally)
titanium (never had the need to take it beyond melting Titanium enriched dust)
Sodium hydroxide (at least until the end game)
Phenol production
Rare earth oxides
Aluminum
copper
glass
I had taken things to heart that "Don't throw anything away because it all feeds into something else." You as a player need to look at the cost benefits on that and see if it makes sense and I can get into the reasons why in my diatribe of "War and Peace."
Let's talk about the 500 lb gorilla in the room and it is salt. Every time I install a patch, there is salt added to it. Feel like I am an a Chinese restaurant kitchen with so damned much salt added to the recipes. It is in the desulfurization recipes, sodium sulfate, saline for salt water electrolysis and zipr, nickel and snuck into a few more recipes. Salt mines are great, but 800K only goes so far and they crater. One would think since they are a mined resource you could plop a few ground borers and get them, but alas that piece is missing. So you have to pull rocks with the ground borer, run through a washer for saline, then dehydrate it out. Cumbersome but still semi-effective.
Sulfur is a huge issue. My primary "go to" is to replace the petroleum chain with desufurization processors which not only breaks down the crude in each tier (crude > heavy oil > light oil > petgas > syngas) but gives sulfur and ash as a byproduct. This became very expensive when salt was added to the heavy and light oil recipes. Cost/benefit, which did I need more? A:Sulfur? B: Salt? I needed the sulfur and ash so I moved on. The second area to get sulfur was in the coke oven gas. This chain was one of the biggest mistakes I invested time in and here's why. You feed the coke oven gas into a filter and it needs copper wire and nickel (which requires sulfuric acid) in order to give you outlet gas 01. You feed that into a F.B. Reactor with your precious ethanolamine to get 20 sulfur in return. You feed that into a wet scrubber with 100 acid gas to get 10 sulfur in return You could have run the acid gas through a dehydrator and gotten that and then nickel required in the first step is a wash with what is required to make the nickel. Next step mix with tail oil for aromatics, then next for some flue gas you can turn into syngas. Trust me, slap a tailings pond on the end of your coke oven gas line and be done with it. If you can make enough petgas, channel your excess to to chemical plant and convert that into sulfur. Wish there was a ground borer option for sulfur as well.
Sulfuric acid. OMG that stuff is needed everywhere and you can't make enough if it. Back the to the sulfur issue. As soon as possible you need to be on the FTS Reactor recipe that yields 500 sulfuric acid and gives you aromatic to boot, but requires a lot of acid gas. The primary method I use is with my desulfurization complex. I feed out the syngas into rectisols where I crack it into refined syngas and acid gas. The refined syngas is then used with sulfur in a gas processing unit to yield more acid gas that feed into the FTS reactor. The second method is that I generate tons of tailing from all the washing facilities I have setup to produce pure sand. I have Evaporators that give off tailings and acid gas which I can then feed into the FTS reactor. Do not try the biofilm route as it will exhaust your biofilm supply.
Methanol is always breaking due to the recipes. "Methanol acquired the name wood alcohol because it was once produced chiefly by the destructive distillation of wood." Honestly, this should have been your base recipe, but the gasifier with nexelit is close and my favorite, when it works. The filtering of waste water is a good method. The use of copper, zinc and syngas is another good method. I don't use the methods requiring nickel due to its already high demand. The Olefins to methanol is great when it works and there is no shortage of zinc chloride.
Nickel. I can't keep up on the nickel production. I get hammered on either the methanol cracking the overflow, biofilm converting the prepared solution in to high grade nickel, or I run out of diesel or sodium sulfate running into the direct reduction units. It's an issue that keeps feeding onto itself. Without the direct smelting of nickel ore the entire chains would collapse because of nichrome.
Nichrome. This is used in so many different things. As soon as the nickel chain comes to a stop, nichrome comes to a stop and anything dependent on it is in a wait state. Without it, you can't make kerosene and your oleochemicals production is shut down. I cannot make enough nickel to feed the 16 high pressure furnaces that are trying to provide for the map. Does the recipe really need to be 10 nickel and 8 chromium to get you 1 nichrome? A little excessive on the recipe?
Biofilm: Biofilm breaks down for one simple reason, and that is in the rayon production which is hampered by one ingredient, carbonyl sulfide. Not much to it, but it needs sulfur, and lots of it. There is another recipe with reslin and sub-denier microfiber, but those are also expensive to get just to make biofilm and it is part of the tin 4 issue.
Nexelit. Now, this one is interesting. I shouldn't have any issues whatsoever with nexelit, but I do! I can get raw nexelit from evaporating tailings, ground borer, or the big mine on a reserve. One of the easiest things to get, but still so problematic. I find myself either smelting the raw or washed nexelit to keep the game going because I never seem to be able to run batches of the molten nexelit because I am out of glycerine or oleochemicals due to nichrome shortages, sodium chlorate because I have blow out another salt mine the chain was setup on, ran out of acetone, or the Armac 12 is depleted due to lead or oleochemicals, or my methanol supply died again.
Zinc: my first gripe was why am I dumping 20 iron sticks for every 1 ore into a ball mill? Was so happy to see that it is now 5-5 in the recipe. MUCH BETTER! And you removed sand castings from the molten zinc recipe. Where I keep getting hung up is on cresylic acid and Aerofloat 15. The cresylic is a victim of the nexelit shortage and the aerofloat 15 is a victim of the sulfur shortage in creating phosphorous pentasulfide. The PP issue can be eased by using pyrite which is generated in the raw coal processing, however, you will need that later as you process High Ash fines.
Lead: 2 break points in it. The first is the nichrome shortage for oleochemicals, already explained. The second is the Z-3 Reagent. The formula was changed on them. The methanol shortage definitely is a factor, but it also now needs carbonyl sulfide. I pulled that from the same feed that was going into my rayon production and now I have neither due to the sulfur shortcomings.
Niobium. I can say I definitely liked it better when it required nitrogen instead of the current ammonia recipe. I chose coke fluidation using 8 F.B. reactors to get the ammonia. Takes more of a hit on your copper supply and coke, but you get tar and tail oil in the trade off. Crack the tar back to coal gas > syngas > refined syngas and feed it into the niobium mines. Tail oil becomes useful because you can then run it through fluid separators for light oil, benzene and aromatics. Combine the benzene and aromatics to make xylenol. The excess light oil from the tail oil separator can go into a desulfurization unit to make petgas and that can go into a chemical plant to create more sulfur.
Grade 4 tin. Now this is the biggest pains that I have been hoping would be fixed but is still an issue. Tin is one of my biggest uses of real estate in the game. I use 10 Automated screeners to turn the tin ore into grade 1&2. 10 jaw crushers to turn the grade 2 into grade 1. 10 more screeners to turn the grade 1 to grade 3. Then 10 washers to turn 1 grade 3 into 1 grade 4. So far so good? Then we feed it into the vanadium chain. 15 grade 4 tin will get you 10 phytoplankton. It will take you 25 phytoplankton to get you 100 alien bacteria. Then its a 1-1 on the alien bacteria to ethanolamine and 80 to make 1 reslin. Or if you feed the phytoplankton into the Xyhiphoe chain, that will require 30 phytoplankton to make 20 Xyhiphoe blood. I have no grade 4 tin to turn into tin, it is all being fed into the phytoplankton. If I weren't feeding into the phytoplankton, then yes, the tin cycle would be balanced. There is no way I could have progressed with out the ability to generate more Aluminum Tailings to convert into Vanadates to supply my needs of Vanadium.
Ok..enough griping about what I had as issue, here is the good stuff.
Chromium. I used a combination of the old extraction from the sand to get chromite for the initial charge of chromium into the system. Once I was able to mine the chromium ore and take it through the full cycle of sintering, I have had warehouses full of chromium and not once did I run out. This was extremely well balanced example of "set it & forget it". I had to go through the full cycle in order to get gold and never had one issue once initially configured and set out. (except for one of the updates which caused a replumb)
Rare earth oxides. The beauty of this is I really didn't need to mine the rare earth bolides and actually shut down that leg after I started converting stone into tar and needed some place to dispose of the rare earth mud. Once converted into the rare earth solution, when fed into the evaporators with sufuric acid, I got a significant amount of copper plates with the rare earth concentrate. After feeding the rare earth concentrate into the solid separator, I had a good supply of iron oxide to feed into the recipes that required them.
Tailings disposal. Don't put the tailings down a sinkhole, they are too valuable! They can be used to make raw nexelit, converted into coal water slurry to be fed into benzene or a combustion mixture. They are also essential to run through an evaporator to create acid gas for the sulfuric acid cycle. But there will be way too many tailing dust to deal with. What to do with those? Pull them into a requester storehouse and feed into classifiers. This will give you iron and copper ore plus a lot of coal dust. You can feed that coal dust into an ammo-loader worker chest and let it power any building that requires fuel. From that point just smelt the ores for a secondary supply of copper and iron plates if there is a blockage in those chains. There is still an overload of coal dust that can be disposed of in a High-pressure furnace and converted to ash.
Just a few game play notes, this was a great integration of the entire Py suite of mods. The one issue with is is the Pycoal and PyOre had the ability to upgrade the buildings. The buildings from fusion did not have the abilities for upgrades and were a bottle neck. Doesn't matter if you upgrade the buildings behind it, if you have Automated Screeners in the front leg, that is your speed moving forward. Only option is to stuff modules, but that tends to hide the production issues and when everything has modules, your bottlenecks come back.
Areas that need I found need addressing:
Salt
Sulfur
Grade 4 tin
Nichrome recipe
This is a great mod set, I love playing it, and you keep getting closer to perfection with every update.
I have tried to make this mod work since the day you first released. I have been there riding one release after the next, trashing a map and restarting because the technology chains changed, dumping 100+ hour maps and restarting. The after patching joys of finding that a full ore processing or chemical chain had suddenly broken because the formulas had changed (making blueprints worthless) and requiring a full replumb to make it work. My goal was to reach the finish line without stuffing the buildings with modules in order to compensate for the deficiencies and bring this mod into full homeostasis where it would all just work. With this current map at 240 hours, I gave up and launched the rocket just to end it.
I wanted to see if this mod could stand on its own. For transparency, the few mods I kept active to run this mod was:
ChargeTransmission
DeadlockLoaders
Loader-Furnace
NoEmptyBarrels
OmegaDrill
Restack
ammo-loader
pycoalprocessing
pyfusionenergy
pyhitech
pyindustry
pyrawores
These are the trouble points that kept breaking no matter what I put into place:
Nickel
salt
methanol
Sulfur
Sufuric Acid
filtration media
biofilm
Grade 4 tin
zinc
lead
nichrome
nexelit
Vanadium
Things that just worked like a champ:
chrome production (had more chrome than a Harley Davidson national rally)
titanium (never had the need to take it beyond melting Titanium enriched dust)
Sodium hydroxide (at least until the end game)
Phenol production
Rare earth oxides
Aluminum
copper
glass
I had taken things to heart that "Don't throw anything away because it all feeds into something else." You as a player need to look at the cost benefits on that and see if it makes sense and I can get into the reasons why in my diatribe of "War and Peace."
Let's talk about the 500 lb gorilla in the room and it is salt. Every time I install a patch, there is salt added to it. Feel like I am an a Chinese restaurant kitchen with so damned much salt added to the recipes. It is in the desulfurization recipes, sodium sulfate, saline for salt water electrolysis and zipr, nickel and snuck into a few more recipes. Salt mines are great, but 800K only goes so far and they crater. One would think since they are a mined resource you could plop a few ground borers and get them, but alas that piece is missing. So you have to pull rocks with the ground borer, run through a washer for saline, then dehydrate it out. Cumbersome but still semi-effective.
Sulfur is a huge issue. My primary "go to" is to replace the petroleum chain with desufurization processors which not only breaks down the crude in each tier (crude > heavy oil > light oil > petgas > syngas) but gives sulfur and ash as a byproduct. This became very expensive when salt was added to the heavy and light oil recipes. Cost/benefit, which did I need more? A:Sulfur? B: Salt? I needed the sulfur and ash so I moved on. The second area to get sulfur was in the coke oven gas. This chain was one of the biggest mistakes I invested time in and here's why. You feed the coke oven gas into a filter and it needs copper wire and nickel (which requires sulfuric acid) in order to give you outlet gas 01. You feed that into a F.B. Reactor with your precious ethanolamine to get 20 sulfur in return. You feed that into a wet scrubber with 100 acid gas to get 10 sulfur in return You could have run the acid gas through a dehydrator and gotten that and then nickel required in the first step is a wash with what is required to make the nickel. Next step mix with tail oil for aromatics, then next for some flue gas you can turn into syngas. Trust me, slap a tailings pond on the end of your coke oven gas line and be done with it. If you can make enough petgas, channel your excess to to chemical plant and convert that into sulfur. Wish there was a ground borer option for sulfur as well.
Sulfuric acid. OMG that stuff is needed everywhere and you can't make enough if it. Back the to the sulfur issue. As soon as possible you need to be on the FTS Reactor recipe that yields 500 sulfuric acid and gives you aromatic to boot, but requires a lot of acid gas. The primary method I use is with my desulfurization complex. I feed out the syngas into rectisols where I crack it into refined syngas and acid gas. The refined syngas is then used with sulfur in a gas processing unit to yield more acid gas that feed into the FTS reactor. The second method is that I generate tons of tailing from all the washing facilities I have setup to produce pure sand. I have Evaporators that give off tailings and acid gas which I can then feed into the FTS reactor. Do not try the biofilm route as it will exhaust your biofilm supply.
Methanol is always breaking due to the recipes. "Methanol acquired the name wood alcohol because it was once produced chiefly by the destructive distillation of wood." Honestly, this should have been your base recipe, but the gasifier with nexelit is close and my favorite, when it works. The filtering of waste water is a good method. The use of copper, zinc and syngas is another good method. I don't use the methods requiring nickel due to its already high demand. The Olefins to methanol is great when it works and there is no shortage of zinc chloride.
Nickel. I can't keep up on the nickel production. I get hammered on either the methanol cracking the overflow, biofilm converting the prepared solution in to high grade nickel, or I run out of diesel or sodium sulfate running into the direct reduction units. It's an issue that keeps feeding onto itself. Without the direct smelting of nickel ore the entire chains would collapse because of nichrome.
Nichrome. This is used in so many different things. As soon as the nickel chain comes to a stop, nichrome comes to a stop and anything dependent on it is in a wait state. Without it, you can't make kerosene and your oleochemicals production is shut down. I cannot make enough nickel to feed the 16 high pressure furnaces that are trying to provide for the map. Does the recipe really need to be 10 nickel and 8 chromium to get you 1 nichrome? A little excessive on the recipe?
Biofilm: Biofilm breaks down for one simple reason, and that is in the rayon production which is hampered by one ingredient, carbonyl sulfide. Not much to it, but it needs sulfur, and lots of it. There is another recipe with reslin and sub-denier microfiber, but those are also expensive to get just to make biofilm and it is part of the tin 4 issue.
Nexelit. Now, this one is interesting. I shouldn't have any issues whatsoever with nexelit, but I do! I can get raw nexelit from evaporating tailings, ground borer, or the big mine on a reserve. One of the easiest things to get, but still so problematic. I find myself either smelting the raw or washed nexelit to keep the game going because I never seem to be able to run batches of the molten nexelit because I am out of glycerine or oleochemicals due to nichrome shortages, sodium chlorate because I have blow out another salt mine the chain was setup on, ran out of acetone, or the Armac 12 is depleted due to lead or oleochemicals, or my methanol supply died again.
Zinc: my first gripe was why am I dumping 20 iron sticks for every 1 ore into a ball mill? Was so happy to see that it is now 5-5 in the recipe. MUCH BETTER! And you removed sand castings from the molten zinc recipe. Where I keep getting hung up is on cresylic acid and Aerofloat 15. The cresylic is a victim of the nexelit shortage and the aerofloat 15 is a victim of the sulfur shortage in creating phosphorous pentasulfide. The PP issue can be eased by using pyrite which is generated in the raw coal processing, however, you will need that later as you process High Ash fines.
Lead: 2 break points in it. The first is the nichrome shortage for oleochemicals, already explained. The second is the Z-3 Reagent. The formula was changed on them. The methanol shortage definitely is a factor, but it also now needs carbonyl sulfide. I pulled that from the same feed that was going into my rayon production and now I have neither due to the sulfur shortcomings.
Niobium. I can say I definitely liked it better when it required nitrogen instead of the current ammonia recipe. I chose coke fluidation using 8 F.B. reactors to get the ammonia. Takes more of a hit on your copper supply and coke, but you get tar and tail oil in the trade off. Crack the tar back to coal gas > syngas > refined syngas and feed it into the niobium mines. Tail oil becomes useful because you can then run it through fluid separators for light oil, benzene and aromatics. Combine the benzene and aromatics to make xylenol. The excess light oil from the tail oil separator can go into a desulfurization unit to make petgas and that can go into a chemical plant to create more sulfur.
Grade 4 tin. Now this is the biggest pains that I have been hoping would be fixed but is still an issue. Tin is one of my biggest uses of real estate in the game. I use 10 Automated screeners to turn the tin ore into grade 1&2. 10 jaw crushers to turn the grade 2 into grade 1. 10 more screeners to turn the grade 1 to grade 3. Then 10 washers to turn 1 grade 3 into 1 grade 4. So far so good? Then we feed it into the vanadium chain. 15 grade 4 tin will get you 10 phytoplankton. It will take you 25 phytoplankton to get you 100 alien bacteria. Then its a 1-1 on the alien bacteria to ethanolamine and 80 to make 1 reslin. Or if you feed the phytoplankton into the Xyhiphoe chain, that will require 30 phytoplankton to make 20 Xyhiphoe blood. I have no grade 4 tin to turn into tin, it is all being fed into the phytoplankton. If I weren't feeding into the phytoplankton, then yes, the tin cycle would be balanced. There is no way I could have progressed with out the ability to generate more Aluminum Tailings to convert into Vanadates to supply my needs of Vanadium.
Ok..enough griping about what I had as issue, here is the good stuff.
Chromium. I used a combination of the old extraction from the sand to get chromite for the initial charge of chromium into the system. Once I was able to mine the chromium ore and take it through the full cycle of sintering, I have had warehouses full of chromium and not once did I run out. This was extremely well balanced example of "set it & forget it". I had to go through the full cycle in order to get gold and never had one issue once initially configured and set out. (except for one of the updates which caused a replumb)
Rare earth oxides. The beauty of this is I really didn't need to mine the rare earth bolides and actually shut down that leg after I started converting stone into tar and needed some place to dispose of the rare earth mud. Once converted into the rare earth solution, when fed into the evaporators with sufuric acid, I got a significant amount of copper plates with the rare earth concentrate. After feeding the rare earth concentrate into the solid separator, I had a good supply of iron oxide to feed into the recipes that required them.
Tailings disposal. Don't put the tailings down a sinkhole, they are too valuable! They can be used to make raw nexelit, converted into coal water slurry to be fed into benzene or a combustion mixture. They are also essential to run through an evaporator to create acid gas for the sulfuric acid cycle. But there will be way too many tailing dust to deal with. What to do with those? Pull them into a requester storehouse and feed into classifiers. This will give you iron and copper ore plus a lot of coal dust. You can feed that coal dust into an ammo-loader worker chest and let it power any building that requires fuel. From that point just smelt the ores for a secondary supply of copper and iron plates if there is a blockage in those chains. There is still an overload of coal dust that can be disposed of in a High-pressure furnace and converted to ash.
Just a few game play notes, this was a great integration of the entire Py suite of mods. The one issue with is is the Pycoal and PyOre had the ability to upgrade the buildings. The buildings from fusion did not have the abilities for upgrades and were a bottle neck. Doesn't matter if you upgrade the buildings behind it, if you have Automated Screeners in the front leg, that is your speed moving forward. Only option is to stuff modules, but that tends to hide the production issues and when everything has modules, your bottlenecks come back.
Areas that need I found need addressing:
Salt
Sulfur
Grade 4 tin
Nichrome recipe
This is a great mod set, I love playing it, and you keep getting closer to perfection with every update.
Re: pY Raw Ores Discussion
Phew mate....that was a huge feedback xD hahaha
pyRO is a new mod and its expected to have imbalances and lots of releases to fix stuff and more to come, thanks to heavy players like you and others we are balancing that big mod and soon it will be ok to play as the others in the py suite.
I will take your requests in consideration..but some of them wont be added in the refered mods, but in pyPH. The main reason im doing a different approach in the pyPH is to easy and cover that issues with sulfur for example. The coke technology is useless today after tier 1, but i put it there to be able to use it in pyPH, since we can produce tons of coke using crude oil.
Base ingredients such as tar, acetone, oleochemicals, glycerol, diesel and sulfur will get more ways to produce and/or extract and that alone will solve more than half of your problems. Sulfuric acid will be directly more balanced with the new methods to get sulfur. The same i cant tell about methanol and biofilm, its planned for a possible alienlife mod. But pyPH will open ways to get some indirect methanol too.
Several things you said that i noticed too and it will come in the next release:
The salt mine will be increased.
New tiers for pyFE buildings.
Coal dust production will be reduced.
Tin consumption for phytoplancton.
Say goodbye to the rare-earth from stone heavy distilation.
Things that will be way more used in pyPH:
Titanium
Plastics
Chromium
Sand
Tin
Uranium
Stone
Lead
pyRO is a new mod and its expected to have imbalances and lots of releases to fix stuff and more to come, thanks to heavy players like you and others we are balancing that big mod and soon it will be ok to play as the others in the py suite.
I will take your requests in consideration..but some of them wont be added in the refered mods, but in pyPH. The main reason im doing a different approach in the pyPH is to easy and cover that issues with sulfur for example. The coke technology is useless today after tier 1, but i put it there to be able to use it in pyPH, since we can produce tons of coke using crude oil.
Base ingredients such as tar, acetone, oleochemicals, glycerol, diesel and sulfur will get more ways to produce and/or extract and that alone will solve more than half of your problems. Sulfuric acid will be directly more balanced with the new methods to get sulfur. The same i cant tell about methanol and biofilm, its planned for a possible alienlife mod. But pyPH will open ways to get some indirect methanol too.
Several things you said that i noticed too and it will come in the next release:
The salt mine will be increased.
New tiers for pyFE buildings.
Coal dust production will be reduced.
Tin consumption for phytoplancton.
Say goodbye to the rare-earth from stone heavy distilation.
Things that will be way more used in pyPH:
Titanium
Plastics
Chromium
Sand
Tin
Uranium
Stone
Lead
pY Coal processing mod
Discord: Pyanodon #5791
Discord: Pyanodon #5791
Re: pY Raw Ores Discussion
Thanks Pyanodon!pyanodon wrote: Sat Feb 23, 2019 8:29 pm Phew mate....that was a huge feedback xD hahaha
pyRO is a new mod and its expected to have imbalances and lots of releases to fix stuff and more to come, thanks to heavy players like you and others we are balancing that big mod and soon it will be ok to play as the others in the py suite.
I will take your requests in consideration..but some of them wont be added in the refered mods, but in pyPH. The main reason im doing a different approach in the pyPH is to easy and cover that issues with sulfur for example. The coke technology is useless today after tier 1, but i put it there to be able to use it in pyPH, since we can produce tons of coke using crude oil.
Base ingredients such as tar, acetone, oleochemicals, glycerol, diesel and sulfur will get more ways to produce and/or extract and that alone will solve more than half of your problems. Sulfuric acid will be directly more balanced with the new methods to get sulfur. The same i cant tell about methanol and biofilm, its planned for a possible alienlife mod. But pyPH will open ways to get some indirect methanol too.
Several things you said that i noticed too and it will come in the next release:
The salt mine will be increased.
New tiers for pyFE buildings.
Coal dust production will be reduced.
Tin consumption for phytoplancton.
Say goodbye to the rare-earth from stone heavy distilation.
Things that will be way more used in pyPH:
Titanium
Plastics
Chromium
Sand
Tin
Uranium
Stone
Lead
Looking forward to the updates and will test the hell out of them. Hopefully the next report will say "no issues found!!"
Cheers!
Re: pY Raw Ores Discussion
Tin consumption for phytoplancton will be reduced or increased?pyanodon wrote: Sat Feb 23, 2019 8:29 pm Phew mate....that was a huge feedback xD hahaha
pyRO is a new mod and its expected to have imbalances and lots of releases to fix stuff and more to come, thanks to heavy players like you and others we are balancing that big mod and soon it will be ok to play as the others in the py suite.
I will take your requests in consideration..but some of them wont be added in the refered mods, but in pyPH. The main reason im doing a different approach in the pyPH is to easy and cover that issues with sulfur for example. The coke technology is useless today after tier 1, but i put it there to be able to use it in pyPH, since we can produce tons of coke using crude oil.
Base ingredients such as tar, acetone, oleochemicals, glycerol, diesel and sulfur will get more ways to produce and/or extract and that alone will solve more than half of your problems. Sulfuric acid will be directly more balanced with the new methods to get sulfur. The same i cant tell about methanol and biofilm, its planned for a possible alienlife mod. But pyPH will open ways to get some indirect methanol too.
Several things you said that i noticed too and it will come in the next release:
The salt mine will be increased.
New tiers for pyFE buildings.
Coal dust production will be reduced.
Tin consumption for phytoplancton.
Say goodbye to the rare-earth from stone heavy distilation.
Things that will be way more used in pyPH:
Titanium
Plastics
Chromium
Sand
Tin
Uranium
Stone
Lead
Why u killing rare earth mud from stone distillation? I think its not quite right
I hope u'll find time to make new tiers for buildings from PYHT
Where u planijning to sue more plastics in PYPH pls tell us

Nickname on ModPortal - Naron79
-
- Fast Inserter
- Posts: 170
- Joined: Thu Jan 10, 2019 3:11 pm
- Contact:
Re: pY Raw Ores Discussion
A bit more constructive criticism. I'm still working on circuit 2 but one thing I noticed is how certain mid tier recipes don't make any sense. Nickel is an example, and I think zinc and titanium were lame too. It's just not worth it to spend that many buildings and MW and other materials for a slight reduction in ore usage. So most of my chains are just using tier 1. It seems like the production greatly increases in the last tier but 2 and 3 are often no man's lands.
And for a while I was excited about getting raw coal 3 to use up the course coal. But I looked at it for a while and I have no idea how many sinkholes it would take to dump all the remaining fluid from raw coal 3 but I'm not going to find out. Finally, I wish you could take molydenum further down the chain like the pyro ores to make more plates.
I also don't think it's any fun whatsoever to use up phosphate mines and rare Earth mines and have to move them all the time. Phosphate requires drills and syngas, isn't that enough? Why do I need to spend so much time finding new mines.
Also it would be nice if there was a possible sink for all the zipir byproducts in green science. Good thing you added the nichrome nylon recipe so I don't need to fill up warehouses with meat
. But then I need a metric ton of nickel and chrome for nylon.
And for a while I was excited about getting raw coal 3 to use up the course coal. But I looked at it for a while and I have no idea how many sinkholes it would take to dump all the remaining fluid from raw coal 3 but I'm not going to find out. Finally, I wish you could take molydenum further down the chain like the pyro ores to make more plates.
I also don't think it's any fun whatsoever to use up phosphate mines and rare Earth mines and have to move them all the time. Phosphate requires drills and syngas, isn't that enough? Why do I need to spend so much time finding new mines.
Also it would be nice if there was a possible sink for all the zipir byproducts in green science. Good thing you added the nichrome nylon recipe so I don't need to fill up warehouses with meat
Re: pY Raw Ores Discussion
Feedback from me: all pymods enabled, production science done and all research till then done.
Shortages: methanol, lead
Fixed shortages with just more of everything: nickel, sulfuric acid. Sulfuric acid produced with vanilla recipes from oil. Using one yellow belt of iron.
I feel I have too much: copper, plastic
General feedback: I feel the higher tiers of RO require too much of valuable liquids that make it hard to justify using it. Example high grade lead: cyanic acid, yeah that is expensive with both recipes but manageable. Z3: methanol shortage hit me there. Might be fixable with big nexelit production for more methanol. Etalomine (yellow stuff, spelled wrong) require nichrome (! expensive). Not something I have large quantities of. Soda ash: no problem to make got plenty of ash, tar and stone.
Shortages: methanol, lead
Fixed shortages with just more of everything: nickel, sulfuric acid. Sulfuric acid produced with vanilla recipes from oil. Using one yellow belt of iron.
I feel I have too much: copper, plastic
General feedback: I feel the higher tiers of RO require too much of valuable liquids that make it hard to justify using it. Example high grade lead: cyanic acid, yeah that is expensive with both recipes but manageable. Z3: methanol shortage hit me there. Might be fixable with big nexelit production for more methanol. Etalomine (yellow stuff, spelled wrong) require nichrome (! expensive). Not something I have large quantities of. Soda ash: no problem to make got plenty of ash, tar and stone.
Last edited by host65 on Sun Feb 24, 2019 4:57 am, edited 1 time in total.