Page 7 of 16
Re: Optimized Steam Engine Setup
Posted: Tue May 31, 2016 9:57 am
by Patric20878
Maybe. But once coal fills up the first belt, it'll be at rest for the entire period between then and coal reaching the last boiler, which should be enough time I think.
Re: Optimized Steam Engine Setup
Posted: Tue May 31, 2016 12:47 pm
by Shokubai
I've been using a similar version of this for a while now. I do not weave belt inside though. I just have inserters take from one boiler to the next. I currently have one belt that feeds the first row of boilers and then 19 behind that which take from each other. For power I user a gap of 1 pipe at regular intervals to insert a pole of some nature.
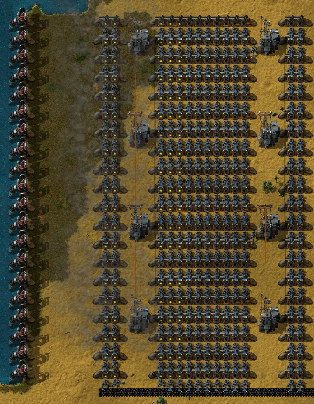
- 2016-05-31 07_52_32-Factorio 0.12.33.png (302.84 KiB) Viewed 12538 times
It's more compact with standard poles and a 1 space pipe but I wanted to see what it was like this way.
Re: Optimized Steam Engine Setup
Posted: Tue May 31, 2016 2:07 pm
by BlakeMW
I figured out a 3/42/30 which is fully tileable, low tech, and uses strings of 21 boilers.
It works at 100% except it suffers the usual flaw that when started under full-load in certain orientations it fails to stabilize at 100%. It will stabilize once allowed to fill with water. My previous attempts at smallpump-less designs with 21 boilers didn't work, but this one does. Water should be delivered using at least 2 pipes, they can be pretty long.
Since i was examining it closely, I figured out more about the "cold start" problem. When the power plant is started under full load,
either by introducing water into empty pipes,
or by introducing coal to empty boilers it will fail to reach it's potential. If the water supply is poor (i.e. long pipes) it can be as low as 12.7MW (83%) and gets much closer to 100% with a better water supply (very short pipes or 3 pipes from the offshore pumps). If load is reduced to under 100% it will successfully stabilize and after that run properly as long as the pipes can deliver enough water.
The full load cold/empty start problem
does not occur if the powerplant is generally orientated East to West or South to North (built with the offshore pumps on the south or east coast).
I'm not sure how seriously to take the "full load cold/empty start" problem, for a start it afflicts the 1/14/10 just as badly as any other design. In real games it's unlikely to happen with the exception of undersized backup steam, or perhaps after a death spiral in a purely steam powered factory. In the case of backup steam it can be avoided by orientating any steam setup East to West or South to North. It is much worse if the water supply is "poor" in terms of pipe capacity (i.e. the offshore pumps are trying to push water through a pipe system with barely enough capacity). My recommendation when testing power plant designs would be to allow them to stabilize under less than full load, before doing a full load test, as a cold/empty start under full load does not reveal flaws in a power plant design.
edit: fixed typo
Re: Optimized Steam Engine Setup
Posted: Tue May 31, 2016 3:15 pm
by Qon
BlakeMW wrote:I figured out a 3/42/20 which is fully tileable, low tech, and uses strings of 21 boilers.
3/42/30
That's a nice design. I'll use it when I build my powerplant. Thanks. It's also smaller than my design somehow.
I'll use blue for the vertical belt and medium poles instead though since I dislike small poles and I'm going to need several parallell belts for coal input anyways.
Re: Optimized Steam Engine Setup
Posted: Tue May 31, 2016 6:35 pm
by Aru
BlakeMW wrote:I figured out a 3/42/30 which is fully tileable, low tech, and uses strings of 21 boilers.
It works at 100% except it suffers the usual flaw that when started under full-load in certain orientations it fails to stabilize at 100%. It will stabilize once allowed to fill with water. My previous attempts at smallpump-less designs with 21 boilers didn't work, but this one does. Water should be delivered using at least 2 pipes, they can be pretty long.
Since i was examining it closely, I figured out more about the "cold start" problem. When the power plant is started under full load,
either by introducing water into empty pipes,
or by introducing coal to empty boilers it will fail to reach it's potential. If the water supply is poor (i.e. long pipes) it can be as low as 12.7MW (83%) and gets much closer to 100% with a better water supply (very short pipes or 3 pipes from the offshore pumps). If load is reduced to under 100% it will successfully stabilize and after that run properly as long as the pipes can deliver enough water.
The full load cold/empty start problem
does not occur if the powerplant is generally orientated East to West or South to North (built with the offshore pumps on the south or east coast).
I'm not sure how seriously to take the "full load cold/empty start" problem, for a start it afflicts the 1/14/10 just as badly as any other design. In real games it's unlikely to happen with the exception of undersized backup steam, or perhaps after a death spiral in a purely steam powered factory. In the case of backup steam it can be avoided by orientating any steam setup East to West or South to North. It is much worse if the water supply is "poor" in terms of pipe capacity (i.e. the offshore pumps are trying to push water through a pipe system with barely enough capacity). My recommendation when testing power plant designs would be to allow them to stabilize under less than full load, before doing a full load test, as a cold/empty start under full load does not reveal flaws in a power plant design.
edit: fixed typo
That is very nice. And, I don't worry about the cold start. The only time it affected me, I was too new to the game to be interested in browsing the forums (and finding layouts like this) anyway. Most people I think, that want to experience the game some before exploring forums and finding these designs, will already be at the point that it won't happen to them, or they'll know how to deal with it better if it does (disconnect the base, manually feed fuel, connect to drills on coal patch, have a chest with red slots on each resource line for collecting and manual grabbing, including coal). I don't remember exactly the parameters of the calculation, so I'm not sure if it carries over, but the power ratio for operating orange inserters fast enough to fully fuel all engines was about 11%. (I think the relevant parameter is the 14:10 ratio.) So, my layout is still exactly the one I developed before being spoiled by any source of information except in-game testing, the same design that you see earlier in this thread, with all orange inserters. I said in this thread, and the TDT thread, that it was inspired by existing steam engine layouts, but I lied cause I was trying to be polite. I see now that it was totally unnecessary politeness. Patric saw my layout within a day of it being posted, and changed out his design in the first post within 5 days (Patric: "Dang, I see my thread made history to still have posts on it almost 15 months later lol. Haven't been here for over a year"....

). He deleted the original images (at least 3 of them, from the image host) (I wonder if he'll delete this one too, that someone put on the wiki), personally I would have just moved them to the bottom of the post and put them in a spoiler, at the most, since it inspired so much conversation, and the thread doesn't make much sense without seeing them. He had a few intermediate replacements, each one a little better. The most coincidental insight, was the offset of the pipe on every other engine row. Or rather, every third row here, every other row on mine, and I used an inserter on the opposite side instead of a red on the same side. I think this has at least been a productive and worthwhile thread, despite the distasteful contention. The back-and-forth, and analysis, is pretty similar to the most productive cooperative engineering groups I've ever been in. (edit: And like I suggested earlier in the thread, the designs gradually kind of converged, they look far more similar now.)
Patric's 'almost 15 month' old (I re-uploaded because it has since been deleted from wiki.factorio.com/images/Compact_power_plant_2.jpg):

Mine from page 2:
And, the death spiral, isn't really there... I had a misconception about the interpretation of that calculation from earlier, because I was focusing more on looking at it from the positive side. (Because, Patric mentioned using all burners instead of orange, so I calculated how many you really need to cold start the engines at full speed.) The further the power supply / demand ratio drops under 11%, the slower it is to come back to 11%. At 0 it doesn't happen, at 11% the rest of the climb depends only on fuel availability. The point of that silly quadratic equation earlier, is to calculate how many burner inserters you need to push the ratio to 11% (including the contribution of the slowed-down orange ones), assuming power demand is matched to (or less than) peak engine output.
"Cold start"... that's so much better of a phrase, I wish I'd been using that from the beginning. ...... On second read, I think you might be talking about a totally different cold start issue, oops. About fluid mechanics, not inserter speed under low power.
Anyway, I think using these blueprints, along with blueprint string mod, is starting to spoil the game for me. While I love making the designs, once I have them, the game is less fun. I am wired like a programmer I guess... I want to make it as good as I possibly can, one time, and then re use it over and over. Or, maybe I'm just playing it too much. In part due to the use of these made-in-advance highly optimized designs, I have solar panels coming in before I need more than the 50 engines pictured above. But steam engines, are just so much cheaper per power than panels are. But as the game progresses, the attention required for the logistics of the engines' need for fuel and water, makes them take more time, attention, and management than just laying down panels and accumulators. I think, maybe the research for solar panels should be harder to get.
Re: Optimized Steam Engine Setup
Posted: Tue May 31, 2016 8:02 pm
by Patric20878
@Aru: Funny thing is, the only reason why I still update this thread is because I somewhat see it as a responsibility. I stopped playing Factorio over a year ago and have no plans to do so again. But the whole reason I ever made this thread was to contribute to making the best possible steam engine design, so here I still am doing so instead of playing Touhou or Tekkit Classic instead, heh. If you ever loved some software or game or whatever but found the dev abandoned it long ago, that's the kind of thing I want to avoid doing. I don't think I can entrust anyone else to be dedicated enough to continue improving on a design even long after they quit the game. Also, I didn't like the discussion we had either, but unfortunately like you've found as well, being nice and polite typically doesn't agree with being productive, and well, priorities man. Nothing personal, all professional, mkay?
And eh, I never really saw a need to keep the images once I make better versions of my designs. There's a reason I keep the version number accurate and mention what was in the previous designs. Don't like old versions cluttering my imgur account, but if anyone wanted to see old versions of my setup, they could always ask. I keep archives of all my previous versions of everything all backed up neatly on 3 different sources. No one's asked yet though. And no, I won't delete it from the wiki lol, it's hosted on the wiki, and I only delete the images from my imgur when I think it's obsolete. It's to be organized.
Meaning, if I can get the update I'm working on now to not have any major disadvantage at all compared to current design (v1.2), the current design pics will be replaced too. But it prob ain't happening because fluid mechanics are weird as heck. Until it is (if it is), the new version will be posted on the bottom of the original post. Think of it like stable and experimental release, lol.
Re: Optimized Steam Engine Setup
Posted: Tue May 31, 2016 9:57 pm
by Aru
Qon wrote:
That's a nice design. I'll use it when I build my powerplant. Thanks. It's also smaller than my design somehow.
I'll use blue for the vertical belt and medium poles instead though since I dislike small poles and I'm going to need several parallell belts for coal input anyways.
Thought I'd mention, a yellow belt can support 105 steam engines at full speed. I even tested it after the calculation, there's a picture somewhere with 10 rows of 10 at full load. Yellow belt items per second is 13.392, I have it memorized now, I've used it so much. That, and boilers are 50% efficiency, engines are 510 kW, and coal is 8 MJ each. And boilers produce 390 kW of heat. So, for 30 engines, you only need 510*30/390= ~39.231, 40 boilers, not 42.
Belt transport system
Transport belt experiments
Re: Optimized Steam Engine Setup
Posted: Tue May 31, 2016 10:15 pm
by BlakeMW
Aru wrote: The back-and-forth, and analysis, is pretty similar to the most productive cooperative engineering groups I've ever been in.
And, the death spiral, isn't really there...
This seems to be true. I usually go all-electric inserters to save fuel and use fasts when pulling from belts (yellows for direct feed between boilers), often if you have any power at all the system can bootstrap itself because all the inserters move in tandem - sure it may be snail pace, but they all pick up a coal and slowly make their turn. Then suddenly a whole lot of boilers light up simultaneously, bringing the system to a healthy power level. I've tested this with designs with like 160 steam engines, connecting them up to a full load, then placing a single solar panel to bootstrap the system, which is like 0.1% power.
0.13 is going to change things, I imagine the rapid inserter will be extremely power-friendly and able to operate at a very low power level (that is I expect the belt will do most the work of loading a bunch of coal into the hand), in general designs with a lot of direct feed between boilers will probably go with fast and rapid inserters and burners will fall out of favor since the lack of stack bonus will cause them to burn even more fuel.
"Cold start"... that's so much better of a phrase, I wish I'd been using that from the beginning. ...... On second read, I think you might be talking about a totally different cold start issue, oops. About fluid mechanics, not inserter speed under low power.
I like "black start" for starting with no electricity as it's the correct term IRL, and I'm tending towards "cold start" for starting the system full of cold water (or no water).
Anyway, I think using these blueprints, along with blueprint string mod, is starting to spoil the game for me. While I love making the designs, once I have them, the game is less fun.
I do not use other people's blueprints for that reason, though I draw inspiration from them. I do use my own blueprint strings for refining setups (because they require so much design) and large steam power plants. Most blueprints I make on the fly.
I'm very fond of solar/steam as a compromise between steam and solar/accu, because you cut the non-blueprintable parts of steam, that is water and fuel supply, by 70%. You need no accus which is nice for saving oil and require 30% fewer solar panels because you don't need to charge accus. Death spiral and black start problems totally go away because your factory is fully powered during the day. You have 30% of your power generation as baseline (always available) meaning you only get brownouts if you over-extend, which is great for lasers.
I also don't have a ploppable solar blueprint w/integrated roboport. Nope. I just have like 10 roboports in the power armor and lay down the solar fields personally. I've used solar/accu blueprints before, but they're really really boring.
Re: Optimized Steam Engine Setup
Posted: Tue May 31, 2016 10:25 pm
by Aru
I also only use my own blueprints. For now, that's... oil processing, research, solar/accumulator array, and smelter lines. (Oh, and a turret blueprint, I think it's 89 items, for 9 personal roboports. It's for combat use, not defense.) Next up, is probably some kind of inclusive blueprint for production of intermediate items for personal use. The oil processing has cracking stuff, but the input pipes aren't connected, so I set up the storage and control scheme without a blueprint. I have a constant combinator where I set the number of tanks for each fluid, and the lower and upper storage thresholds as percentages for cracking. So, if I set it to 20 and 99, it'll crack A into B if: A is 99% or higher, in order to keep the refineries going, or B is under 20%.
Solar
Research
(I added a note about boilers in the post above)
Re: Optimized Steam Engine Setup
Posted: Tue May 31, 2016 11:17 pm
by Qon
Aru wrote:
Anyway, I think using these blueprints, along with blueprint string mod, is starting to spoil the game for me. While I love making the designs, once I have them, the game is less fun. I am wired like a programmer I guess... I want to make it as good as I possibly can, one time, and then re use it over and over.
I think it's nice to solve one part. There's more things to solve anyways so I don't have to solve the same thing over and over again. I think that would be boring.
Also there's challenges and challenge mods if you want to make all your designs and patterns useless. Right now one of my playthroughs is a burner only factory, no electric grid. It's not actually as tedious as that mihgt sound, it's still automatable. I have burner leech mod which means burner inserters can pull coal from burner units and from belts if necessary, and burner assembly machines. For the things that there's no burner equivalent machine to I pipe hot water instead of wire electricity and place steam engines next to the electric machine connected with poles without wires. I gets a bit tricky sometimes because you almost always need half the belt you pull from to have coal on (so you can't have multiple input ingredients) it and you don't have any fancy long inserters to reach several belts.
Aru wrote:
Thought I'd mention, a yellow belt can support 105 steam engines at full speed. I even tested it after the calculation, there's a picture somewhere with 10 rows of 10 at full load. Yellow belt items per second is 13.392, I have it memorized now, I've used it so much. That, and boilers are 50% efficiency, engines are 510 kW, and coal is 8 MJ each. And boilers produce 390 kW of heat. So, for 30 engines, you only need 510*30/390= ~39.231, 40 boilers, not 42.
Then a blue belt would support ~300 steam engines at 150MW. Sounds like I need like 20 blue belts of coal then. And that is before I start to my explosive expansion that will occur as soon as my 1 minute rocket factory is blueprintable for rocket spam on a massive scale. But thanks for the boiler number.
BlakeMW wrote:
I do not use other people's blueprints for that reason, though I draw inspiration from them. I do use my own blueprint strings for refining setups (because they require so much design) and large steam power plants. Most blueprints I make on the fly.
I like doing my own, but for things like your steam setup it's so simple that it would be silly to not do it when I know it without looking at the picture. And I took part in it's design. I'm not going to avoid building a perfect design because someone else has done it also. Of course I will allow myself to make the best factory I can make. If I aquire knowledge from others then I should use it and maybe build on top of it. And It will have to be modified slighty if I want lots of GW out of it so it won't be enough to make and exact copy and plop and forget anyway.
Re: Optimized Steam Engine Setup
Posted: Tue May 31, 2016 11:23 pm
by Patric20878
K, all the kinks worked out on the standard design. 21 boilers and 15 steam engines per row, at 104 blocks long. 5 blocks more compact than Blake's design, at 20.8 tiles per steam engine. Given at least one cold start, will always output 45.9 MW. Pretty satisfied with this design, even if I can't get the battery variant to work, as besides the cold startup requirement, it works pretty cleanly and doesn't introduce any other flaw. Added to original post at the bottom - haven't decided if I want to make this the new setup yet, mainly because I can't get the water battery setup to work with this without dropping output. And actually, I had the standard setup finished like 1.5 days ago, but really wanted to get the water battery variant working too so I could post them both together. But no luck on that.
However, the water battery variant does work if a cold start is given with storage tanks detached, storage tanks are filled, then detached again, then steam engines are connected to power whatever. Then that produces 45.8 MW, connecting the pipes between each 3 offshore pumps actually lowers max output by 0.1 MW. But that's a manual setup, so meh.
I kinda wonder if anyone ever actually builds the water battery variant though, because I sure don't. If anything, coal fields at base are easy to see, and now that I know how to make the coal detector react within 20 seconds or so, coal fields farther from base are easily long enough to give time to setup a new mine. And for very distant mines, train + massive train cargo gives plenty time too. Much rather just build lots of accumulators, which solars eventually need anyways.
Re: Optimized Steam Engine Setup
Posted: Tue May 31, 2016 11:38 pm
by Aru
BlakeMW wrote:I figured out a 3/42/30 which is fully tileable, low tech, and uses strings of 21 boilers.

...
You can compact the engines a bit and use half the poles on them, if you look at my layout on page 14. 4 engines per small pole instead of 2.
Oh... but then, you still have to connect them underneath. But it can't be *more* poles.
Re: Optimized Steam Engine Setup
Posted: Tue May 31, 2016 11:41 pm
by Patric20878
@Aru: Already done. Doubt it's going to get more compact than this lol. See bottom of original post.
It would've been a 14/15 setup like v1.2 is, but it doesn't compact nearly as neatly as 9/10 does. So no longer compacts as well as it does, but uses 15 engines per row, which is also nice.
Re: Optimized Steam Engine Setup
Posted: Wed Jun 01, 2016 12:37 am
by Aru
Before I started browsing designs on the forums, when I was making my engine layout, I was using the offshore pumps as they are here, adjacent to each other without the gaps. Stretches of straight shoreline are valuable, and it helps take advantage of them. There was a cross pipe connecting some of them (I intuitively suspected there were fluid issues like was being talked about above, where flows impede each other, funny), and they were roughly aligned at the center of the engine array. So, I was using the same layout you see here (my layout I mean), but I also had the pumps compressed better (as in, not always aligned with the engine rows), depending on the shape of the lake shore.
That's why my screenshots stop at the open pipe ends of each row, and don't show the offshore pumps. Because sometimes you should squeeze in as many offshore pumps as you can, or follow an irregular shore line, and then pipe them over to the engines. (You can't pipe all the water from one place to another with a single pipe, of course, it's not big enough. But it gives flexibility for different shore shapes, and for better using smaller shore straights.)
Re: Optimized Steam Engine Setup
Posted: Wed Jun 01, 2016 9:36 am
by BlakeMW
Aru wrote:
You can compact the engines a bit and use half the poles on them, if you look at my layout on page 14. 4 engines per small pole instead of 2.
The 4 engine per pole layout is pretty similar to the one I use for solar panels (including the row of connecting poles at the bottom), though usually small power pole conservation is not something I care about much because the things almost literally grow on trees and if a build is a little cleaner with more small power poles that seems acceptable.
I do have a great layout for a quad-row of engines using medium power poles:
That is 6 engines per pole. The ends are "ragged" so it's not going to win any beauty contests, but it's very compact and the pole-efficiency is very good, I'm not sure if it even can be beaten in pole efficiency.
Re: Optimized Steam Engine Setup
Posted: Wed Jun 01, 2016 10:20 am
by Patric20878
My old v1.1 design arranged in triple rows using medium poles matches it in pole efficiency, powering 6 engines per pole also. Aru posted the image earlier.
By the way, see if you can figure a working design with water tanks based off the new design I posted at the end of my original post. I tried attaching small pumps right after the offshore pumps, and while it's highly compact, doesn't produce at full power, even with a cold start. Attaching them right after the boilers doesn't work either, and neither does having them both before and after the boilers. Also, that thing you mentioned about water flowing backwards harming power output...was that referring to the water tanks sending water backwards? Like mentioned, I found that disconnecting them recovers output. Tried putting water tanks before the steam engines, along with also trying small pumps right after the tanks...didn't work at all.
I think I need to get a way to disconnect the water tanks after they're full or something.
Re: Optimized Steam Engine Setup
Posted: Wed Jun 01, 2016 11:34 am
by BlakeMW
Patric20878 wrote:My old v1.1 design arranged in triple rows using medium poles matches it in pole efficiency, powering 6 engines per pole also. Aru posted the image earlier.
By the way, see if you can figure a working design with water tanks based off the new design I posted at the end of my original post.
It's not possible without small pumps. The only "water battery" designs which work use 1/14. The reason is that storage tanks can draw "limitless" water through a boiler string. The 1.5/21/15 design works because the 15 steam engines regulate (limit) the flow through the 21 boilers based on how much a steam engine consumes per second. But a storage tank has no real limit (it's at least as high as 300/s), this will result in more water being sucked through one boiler string than the other.
You can get something which almost kind of works by placing 25 steam engines (or steam engines + pipes) and then the storage tanks, in this case the sheer length of the pipe system limits the flow to a degree. However the problem is if you allow the system to become empty you get serious problems with the flow being too fast because of the voracious appetite of the steam engines and tanks, that results in serious degradation if the powerplant is a west-coaster or mild degradation if it is an east-coaster. So you have a system which kind of works okay if isn't allowed to become empty, but isn't exactly following any proper ratios. Personally I'd stick with the 1/14 designs as found in the link in my sig, they follow ideal ratios and work great.
Though speaking of those designs, they're pretty old and I've built better designs in my factory (just not better enough to bother updating the guide). I designed a new one using everything I've learned which is optimized for perimeter:
That's for solar/steam, it has 68 steam engines whereas the ideal number is 66.67 - having extra steam engines does no harm. When connected to a load which consumes the entire output, and to the same mega-wattage of solar panels the boilers will run at 100% all day long and the water should be steady at 100 degrees. The main feature difference between my older designs is this one has a direction connection from the boilers to both the steam engines and the storage tanks, using a shared water pipe, this direct connectivity is really helpful for ensuring proper filling of tanks and proper direct access to the boilers for the steam engine, it's effectively an increase in parallelism which is always good in these designs, parallelism is great for overcoming pipe capacity problems - much how in electric circuits parallel resistors have reduced resistance. It also uses the "burn the candle from both ends" principle, both ends can provide approximately equal amounts of water flow when the system is under full load.
Btw notice the sneaky long handed inserter? Yes, there is a stealth 29th boiler! Making it a 2/29/68. The reason for the 29th boiler is because when a 1/14 system is under a lot of suction (like from storage tanks) you need at least 15 boilers to heat the water (it means some of the boilers are underutilized due to the water dwell time being too short). The 29th shared boiler seems to work fine to keep the water at 100 degrees and the long-handed inserter and extra boiler just fit in without making the design any larger.
Re: Optimized Steam Engine Setup
Posted: Wed Jun 01, 2016 2:30 pm
by Patric20878
Is there a way to use small pumps to make the 15 steam engine setup work with water tanks? I need to know if there's a way to shut off small pumps once tanks are full, and while combinations can provide for this inverted logic, I can't think of any that can react based on how full a storage tank is, or based on water flow in a pipe.
And if there is no way, I still question if making water tanks is really worth it at all. I originally added it as a feature, but since last year, my consideration for aspects of a factory to optimize also includes ones like time, resources, and others, and I wonder if making all those water tanks is a better idea than making lots of accumulators. What use do massive amount of water tanks still have once the player moves entirely to solar power? If there's no use, it's not an efficient use of time for teching up.
Re: Optimized Steam Engine Setup
Posted: Wed Jun 01, 2016 2:56 pm
by Qon
Patric20878 wrote:Is there a way to use small pumps to make the 15 steam engine setup work with water tanks? I need to know if there's a way to shut off small pumps once tanks are full, and while combinations can provide for this inverted logic, I can't think of any that can react based on how full a storage tank is, or based on water flow in a pipe.
And if there is no way, I still question if making water tanks is really worth it at all. I originally added it as a feature, but since last year, my consideration for aspects of a factory to optimize also includes ones like time, resources, and others, and I wonder if making all those water tanks is a better idea than making lots of accumulators. What use do massive amount of water tanks still have once the player moves entirely to solar power? If there's no use, it's not an efficient use of time for teching up.
Small pump condition: water < 2500. Just wire them to the tanks. That's it.
But the question is, do you want storage tanks? The reason for accumulators with solar panels is because solar stops outputting energy during the night. But with steam you have energy stored as coal as a perfectly valid energy buffer that can be converted to energy as fast as you need it if you have enough steam engines and boilers. Hot water is just another way to store energy. But with hot water you still need a steam engine setup massive enough to handle converting your hot water to electricity. The only advantage really is that you don't need as many boilers when converting from hot water to electricity. So if you onnly use steam engines to handle spikes in energy requirements then you can use less boilers combined with water tanks to slowly fill up the tanks with hot water ready for instant conversion. But if your boiler setup is big enough to heat water as quickly as steam engines use them then hot water storage is pretty useless. Having storage tanks when you have enough boilers is a bit like having solar panels that work at night too and enough to handle any spike, but still insist on crafting expensive accumulators.
Since boilers is actually lower tech than storage tanks I don't really see any reason someone would have lots of storage tanks but not being able to get enough boilers for your power plant. They are cheap as dirt (literally, they are crafted from stone which is used for almost nothing else). And storage tanks instead of boilers don't give you the ability to have high output all the time.
Storage tanks for hot water would be really useful if we had solar panels that heated water instead of being photovoltaics. Or if we had an electric boiler (a mod does this, but it prevents accumulators from working).
Re: Optimized Steam Engine Setup
Posted: Wed Jun 01, 2016 5:00 pm
by Patric20878
I'm inclined to agree. The more I think about it, the less worth it storage tanks seem to be. Just isn't worth using the time making storage tanks instead of accumulators to tech up, and there's no reason you can't just have chests with fast inserters storing coal into chests, then taking them back out when the coal belt is depleted. Since you need a lot of accumulators anyways eventually, it's not really wise to go for compactness with the storage tanks, since then you're trading tech speed for it.
I think I'll probably remove the water battery variant. The standard variant with 15 engines works really well, and it's only flaw with needing to cold startup first is pretty natural to do anyways.