Automated guided vehicles (AGV)
Posted: Tue Nov 27, 2018 8:59 am
I'm sorry, if this kind of suggestion has been made before. I have used the search, but due to my poor English, I may have been used the wrong keywords.
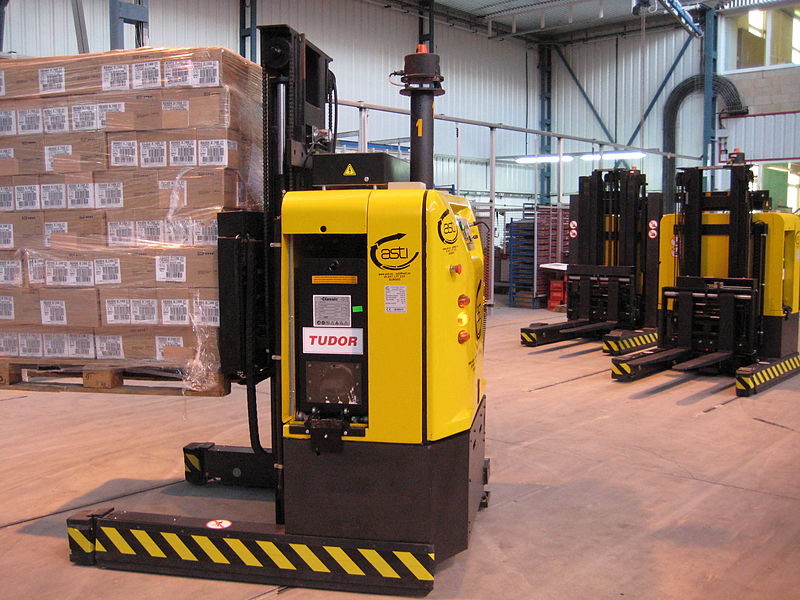
This would be an intermediate transport system for medium sized material flow bound to special lanes. Its like a small sized railway system ( AGV 1x1 tiles, curves 1x1 tiles!) with a inbuilt "pull logic".
Each AGV is dedicated to a single input station and one or more output stations.
An input station consists of a loader, a stack of empty crates and a parking area. 2x2 tiles in size. Additional AGV can be parked there, too (underground ?)
An output station consists of an unloader and a storage for empty crates. An output station can directed to several input stations. But an AGVs can only handle a single route.
During being idle the AGV waits loaded with a crate loaded with goods at its input station (and it is recharging its batteries).
If an dedicated output station signals getting lower than a set minimum threshold, the goods are transported to the output station in need.
On arrival the crate is left there and an empty crate is carried "home".
A crate can only hold a small amount of goods. E.g. 4 stacks.
At the input station you can define a ratio of multiple goods ( not bound to stacks but limited by the capacity of the crates). E.g. 60 gears, 30 iron plates and 120 copper cables.
The AGV can only drive on special paved ways. You can define such a lane as one direction only or both directions. In the case of both directions for a single lane you may need a few evasive bays, if several AGVs are using the same way (e.g. several AGVs are dedicated to the same loading station or the road network consists of crossings).
Unlike trains, the AGVs do not need any signals: If a two directional way is already in use in the opposite direction, the AGV waits in the closest bidirectional double lane or evasive bay. In the case of AGVs driving in the same direction, they can follow each other with a minimum distance.
Belts are good for mass products on short or medium distances. But belts don't have any logic than the "push logic" unless you make use of a large array of signal circuits.
Trains are good for very long distances. But they are too big for distances between production lines.
Logistic robots are good for small amounts of goods on short distance. But unless you mass produce these robots, they can only handle small amounts of goods. They make the setup of the factory too easy, too (IMHO).
There is a gap between these three options to transport material. An AGV ( like I have described above) would fit well to close the gap :
You can handle bigger amounts of materials than robots. They use partly the pull logic of the robots. But you need to setup the threshold values and need to think of the roads for the AGVs.
For the production of not automatically used products without the need of mass production (e.g. new assembly machines, new trains), a different kind of logistic system would be very useful ... IMHO.
TL;DR
Nowadays, there are logistic systems like many types of automated guided vehicles (AGV).What ?
I am thinking of an AGV like this ...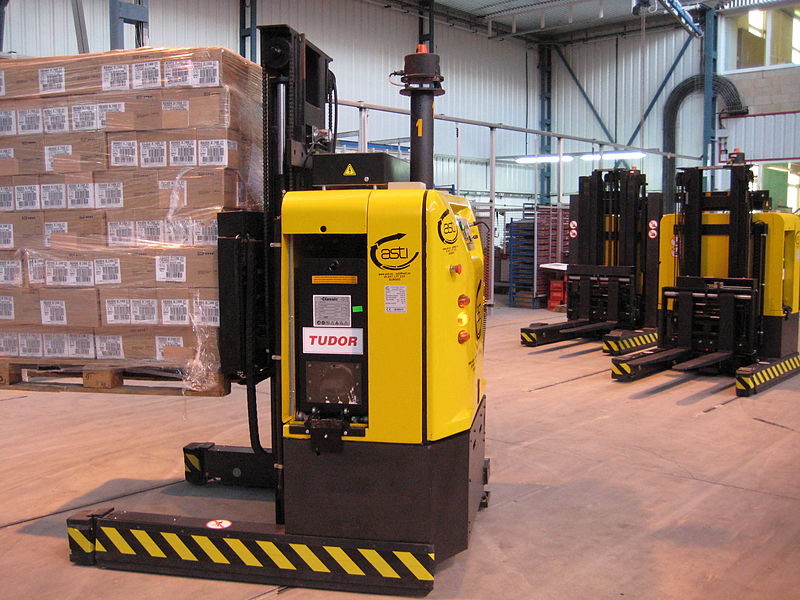
This would be an intermediate transport system for medium sized material flow bound to special lanes. Its like a small sized railway system ( AGV 1x1 tiles, curves 1x1 tiles!) with a inbuilt "pull logic".
Each AGV is dedicated to a single input station and one or more output stations.
An input station consists of a loader, a stack of empty crates and a parking area. 2x2 tiles in size. Additional AGV can be parked there, too (underground ?)
An output station consists of an unloader and a storage for empty crates. An output station can directed to several input stations. But an AGVs can only handle a single route.
During being idle the AGV waits loaded with a crate loaded with goods at its input station (and it is recharging its batteries).
If an dedicated output station signals getting lower than a set minimum threshold, the goods are transported to the output station in need.
On arrival the crate is left there and an empty crate is carried "home".
A crate can only hold a small amount of goods. E.g. 4 stacks.
At the input station you can define a ratio of multiple goods ( not bound to stacks but limited by the capacity of the crates). E.g. 60 gears, 30 iron plates and 120 copper cables.
The AGV can only drive on special paved ways. You can define such a lane as one direction only or both directions. In the case of both directions for a single lane you may need a few evasive bays, if several AGVs are using the same way (e.g. several AGVs are dedicated to the same loading station or the road network consists of crossings).
Unlike trains, the AGVs do not need any signals: If a two directional way is already in use in the opposite direction, the AGV waits in the closest bidirectional double lane or evasive bay. In the case of AGVs driving in the same direction, they can follow each other with a minimum distance.
Why ?
I think, we could use a little bit more variety of logistic systems : Belts, trains and robots do not fit for all purposes.Belts are good for mass products on short or medium distances. But belts don't have any logic than the "push logic" unless you make use of a large array of signal circuits.
Trains are good for very long distances. But they are too big for distances between production lines.
Logistic robots are good for small amounts of goods on short distance. But unless you mass produce these robots, they can only handle small amounts of goods. They make the setup of the factory too easy, too (IMHO).
There is a gap between these three options to transport material. An AGV ( like I have described above) would fit well to close the gap :
You can handle bigger amounts of materials than robots. They use partly the pull logic of the robots. But you need to setup the threshold values and need to think of the roads for the AGVs.
For the production of not automatically used products without the need of mass production (e.g. new assembly machines, new trains), a different kind of logistic system would be very useful ... IMHO.